
In the pulp and paper industry, advanced process pumps are crucial for transporting suspensions at high consistencies, speeds, and pressures continuously. Ensuring these pumps operate smoothly is vital to avoid costly downtime due to unexpected technical failures.
24/7 Remote Monitoring for Enhanced Performance
What if the pumps could be monitored remotely 24/7? What if key parameters could be continuously tracked and anomalies in pump performance analyzed in real-time? What if relevant personnel could be automatically informed in the event of critical performance issues? Then, appropriate action could be taken before costly pump failures occur.
Chesterton has developed state-of-the-art system monitoring devices that do just that – let’s talk about the Chesterton ConnectTM System.
When it does not run smoothly – Chesterton ConnectTM System finds the failure in rotating machinery
When rotating equipment does not run smoothly, the Chesterton ConnectTM System helps identify the failure. The Chesterton ConnectTM System comprises robust, industrial-grade sensors, gateways, and an intuitive cloud dashboard. These sensors and gateways automatically capture and transmit equipment-operating conditions to the Chesterton Connect™ Cloud dashboard in near real-time. This simplifies remote equipment monitoring and enhances operational efficiency.
The Chesterton Connect™ System allows for easy monitoring of mechanical seals and can be easily installed on various types of pumps and mixers equipped with mechanical seals. The following parameters can be monitored and compared around the clock and in near real-time, no matter where you are:
- Process temperature
- Process pressure
- 3-axis Vibration (Acceleration and Velocity RMS)
- Surface temperature
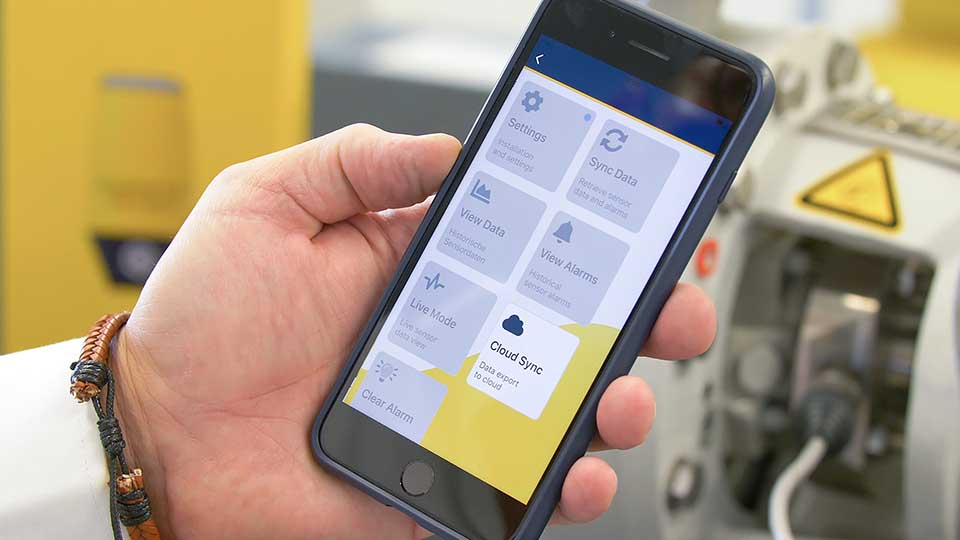
The easy-to-install Chesterton ConnectTM sensors and user-friendly app give you a comprehensive overview of the status of your equipment. By setting thresholds, the mobile app and the device’s LED display system alert you to anomalies. This alert system helps you to take proactive maintenance measures to avoid unplanned downtime and system failures.
Flexible Monitoring Solutions
The Chesterton ConnectTM Sensor can monitor a rotating machine as a single device. With the Chesterton ConnectTM Gateway, up to 50 sensors, i.e. a complete pump park, can be efficiently controlled using the Chesterton ConnectTM Cloud.
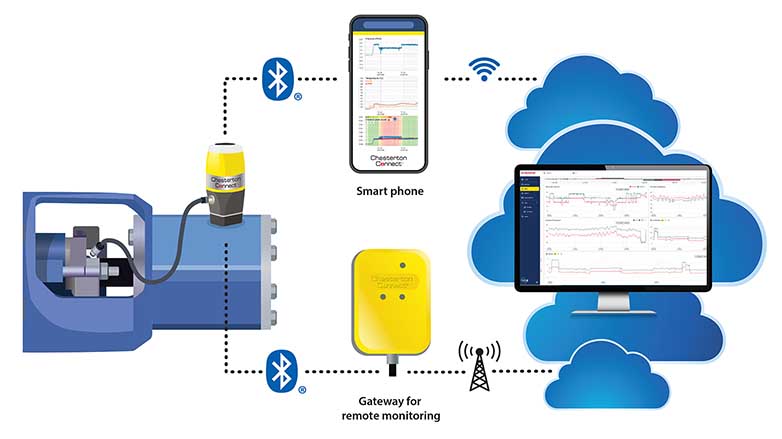
Key features of the Chesterton ConnectTM Cloud Dashboard include:
- Real-time performance alerts, notifications and automatic reports via email or app.
- The ability to monitor overall performance and compare data for up to 50 units per gateway.
- Analysis of deviations, trends or comparison with industry standards.
- Ability to add task notes for streamlined completion.
Through data collection and analysis, the system provides insights that facilitate proactive maintenance planning, minimize downtime and extend the life of your devices.
Proactive maintenance for cost savings
In paper and pulp production, we can help our customers in many ways. In numerous reference cases, the Chesterton ConnectTM System provides support by monitoring the stuffing box pressure, the process temperature, the vibrations and the surface temperature.
Typical applications
One critical application in the process is the monitoring of the flow of stock supplied to the paper machine by the fan pumps. In this application, this is critical as the suction pressure and flow to the pump must be uniform and uninterrupted. Anomalies in the fan pumps can be localized and proactively eliminated before the reliability of the system is compromised or there is a risk of serious damage to the pumps.
Another application is to monitor equipment after it has been installed. It is very common for a poorly fitted mechanical seal, a shaft misalignment problem or a faulty valve to cause failure very quickly. In this case, continuous monitoring of the equipment allows the user to be informed quickly in the event of a malfunction. Without an IIoT monitoring system, it is usually very difficult and time-consuming to find the real error in the system.
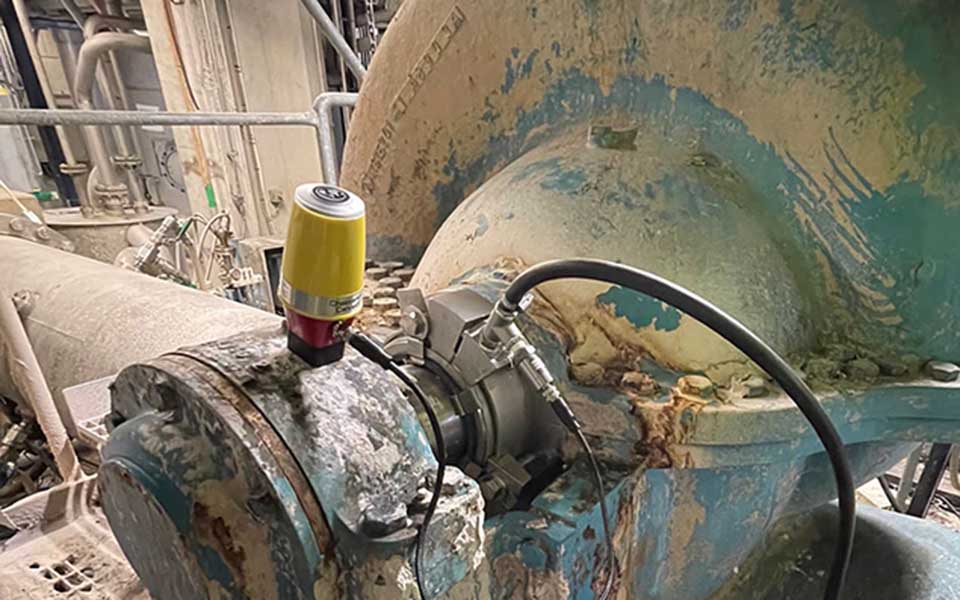
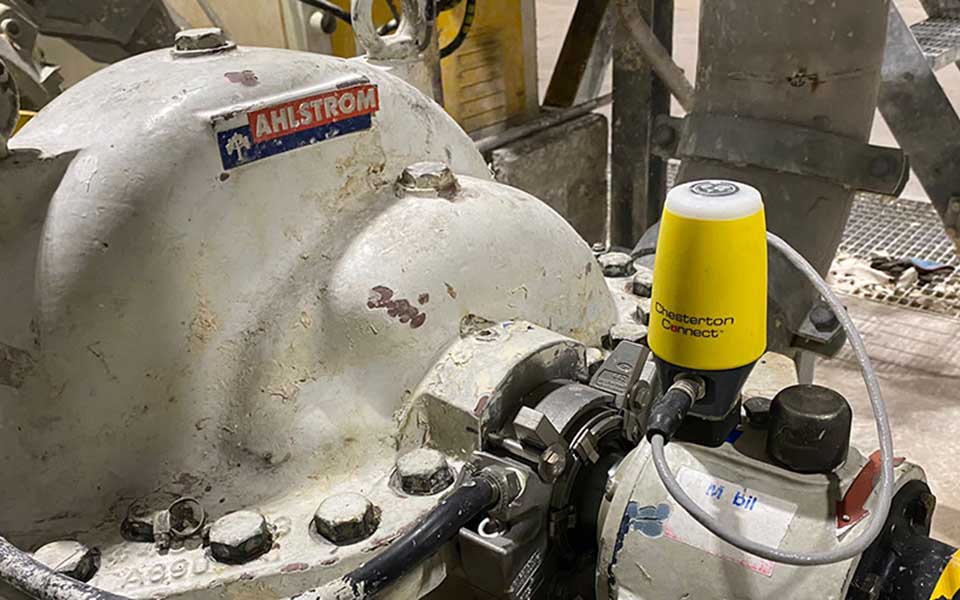
Our interesting case studies will give you an insight into the performance spectrum and possibilities of the Chesterton ConnectTM System:
Chesterton 1510 Seal and Connect Monitoring Increase MTBR
Pump Vibration Issues Identified and Solved with Chesterton ConnectTM
Conclusion
The ability to connect up to 50 wireless Chesterton ConnectTM sensors to one gateway and create a complete monitoring network of multiple gateways enables efficient simultaneous monitoring of a large number of pumps and sealing systems. Give your team unparalleled insight into system health, gain actionable analytics and stay ahead of the competition in today’s rapidly evolving industrial landscape.
Do you have any questions about our IIoT Technology? Please ask our Expert Desk. We gladly assist you.
You can also make a preliminary selection using our product selector. Our product consultants will gladly assist you in selecting the ideal product for your application.