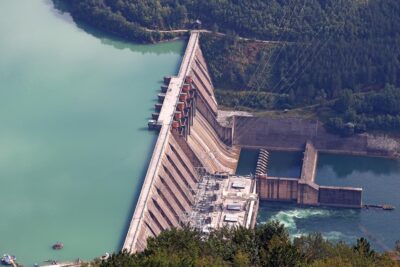
For many years, Chesterton has offered hydropower facilities cost-effective hydraulic and pneumatic sealing solutions that ensure leak-free sealing and increased turbine efficiency. Worldwide, OEMs, operators, and refurbishment businesses rely on our incredibly dependable and high-quality products.
In your cylinders, using a combination of high-performance seals and Chesterton-exclusive materials can significantly reduce total equipment costs, increase mean time between repairs (MTBR), and enhance operating performance. Our flexible manufacturing capabilities allow us to produce almost any design, any material, and any size seal with quick lead times for both molded and machined products.
Chesterton delivers various sealing solutions for cylinders, turbines, and valves in this industry,including:
- Kaplan Blade Runners
- Wicket Gate Cylinders
- Servo Cylinders
- Blade Pitch Cylinders
- Brake and Jack Cylinders
- Butterfly, Spherical, and Ball Valves
Kaplan Turbine – Most common Type of Turbine in Hydropower
The Kaplan turbine is an overpressure turbine. The guide vanes installed in front of the impeller create a swirl in the water. As the water flows through the water turbine, the force of the water acts on the guide vanes. This causes the impeller to rotate.
In addition to the guide vanes, the blades of the Kaplan turbine are also movable and adjustable. This allows the angle of attack to the water flow to be changed. The guide vanes direct the inflowing water so that it hits the blades of the impeller at an optimum angle. This makes it possible to react optimally to fluctuations in the water supply and achieve a high level of efficiency even with a low water volume. Kaplan turbines are ideally suited for use with low heads and large fluctuating flow rates. The Kaplan turbine is therefore predestined for large, run-of-river power plants with low to medium heights of up to 80m.
The Kaplan turbine has around 4 to 8 adjustable runner blades. The adjustability of the blades means that efficiency losses outside of nominal load operation can be kept to a minimum. At 30 percent to 100 percent of the nominal volume flow, the efficiency is around 85 to 95 percent. Therefore, it is no wonder that the Kaplan turbine – named after its inventor Victor Kaplan – has been shaping energy generation from hydropower for more than 100 years.
Sealing Challenges
There are many sealing challenges to overcome that are directly or indirectly associated with the equipment used to generate hydropower. Applying advanced sealing materials and designs can help address some of these challenges by:
- Improving mean time between repairs
- Simplifying installation
- Reducing maintenance costs
- Minimizing downtime
- Positively impacting the environment
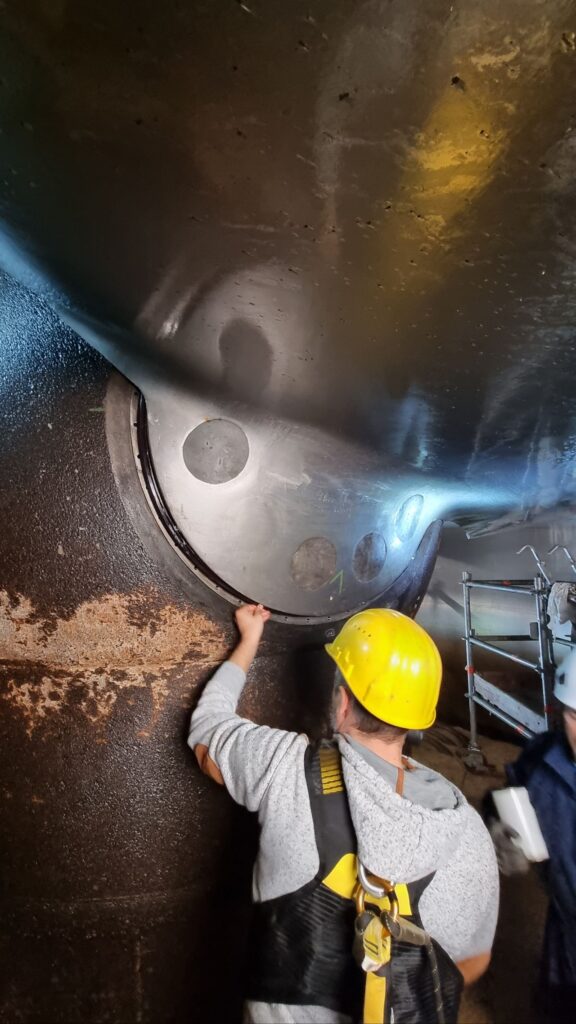
Particularly with Kaplan turbines, runner blade trunnion seals are essential for preserving dependability, effectiveness, and shielding the surrounding area from oil seepage. More than 60% of Kaplan turbine leaks are caused by ineffective or failing blade trunnion seals, according to a survey done among owners of Kaplan turbines.
Common Blade Runner Trunnion Sealing Issues
There are several blade trunnion sealing challenges that need to be considered to establish optimal sealing reliability. They include:
- Failure to keep water/contaminants out of the hub: Poor seal fit or poor seal design and seal material are most often the culprits, along with the impact of factors below.
- Failure to keep oil in the hub: Also due to poor seal fit or poor design and seal material
- Not accounting for blade droop: Due to manufacturing tolerances and running clearances of machined components, there is a certain (natural) droop of the turbine blades.
A common bearing/bushing material for blade trunnion is cast bronze, which has a relatively low stiffness. This can lead to deformation of the bearing under high load, caused by the weight of the blade and by reaction force created on the blade during operation. Such bearing deformation will increase the blade droop value.
The wearout of blade trunnion bearings is the third factor that can affect the blade droop value. When the blade oscillates, boundary friction arises if a stable oil-film between the trunnion and the bearings ring is not maintained. This, combined with a high radial load, might result in excessive wear of the trunnion/bearing assembly.
Blade droop challenges the trunnion seals, changing the original cross-section for which the seals were designed. This must be compensated by the sealing devices as well. Blade droop can have a serious impact on performance, positive sealing, and seal life expectancy.
Such geometrical changes can lead to:
- Radial overload of the seals (in the direction where the seal cavity cross-section has been reduced)
- Radial opening of the seals (in the direction where the seal cavity cross-section has been increased)
- Excessive deformation and friction (wear out of sealing devices)
How can you achieve optimal Runner Blade Trunnion Sealing?
- Get exact turbine/blade measurements
One of the most basic, but often overlooked aspects of selecting runner blade trunnion seals for Kaplan turbines is accounting for the wide variation in turbines and blades when determining the seal size needed. There are no technical specifications or internal standards for designing runner blade seal stuffing boxes. For this reason, and because as equipment dimensions change from the original specification after years of use, make sure you obtain actual equipment dimensions both by turbine and by blades.
- Check the seal cavity cross section values around the blade trunnion
It is important to understand that blade droop plays a factor in these measurements. The typical number of Kaplan runner is 4-8 blades. The natural wear of bearings and consequential blade droop values can vary blade by blade even with the same turbine. The seals should be designed and manufactured individually.
- Check and resolve equipment conditions
Surface conditions and the roughness of dynamic and static counter surfaces have to be considered. These uneven and abrasive surfaces can have an enormous impact on seal device performance and service life.
- Consider operation/environmental conditions
Fluctuation of turbine pressure – water head levels drop and rise, and can periodically change the pressure load on sealing devices. This can have an adverse impact on seal performance and reliability.
Vibration and cavitation – a certain level of vibration and cavitation is standard to the operation of Kaplan turbines, this has a major impact on turbine components, including runner blade trunnion seals. Flexible seal design and elastic seal material can respond to such impact and withstand for a longer time.
Low water heard schemes – Low water head can represent a high risk of abrasive environment caused by water contaminants, sediment, and mud. Using a seal with an abrasion-resistant thermoset polymer material can offset these abrasive effects.
- Select the best runner blade trunnion seal
Advanced hydraulic sealing technology can significantly improve meantime between failures, and reduce meantime to repair. The optimum seal also helps to reduce operational and maintenance costs, lower the risk of unplanned downtime, and lessen downstream pollution.
Chesterton delivers the Ultimate Solution
Chesterton Kaplan Turbine Runner Blade Trunnion Split Seal –
High-Performance Split Lip Seal for Heavy Duty Rotary and Oscillating Applications
Specifically for Kaplan Turbines, Chesterton invented innovative Kaplan Runner Blade Trunnion Split Seals – high-performance lip seals for heavy-duty, dynamic rotary and oscillating seals applications in the hydropower industry. These seals are specifically designed for the Kaplan (or “propeller Type” turbine runner blade trunnions.
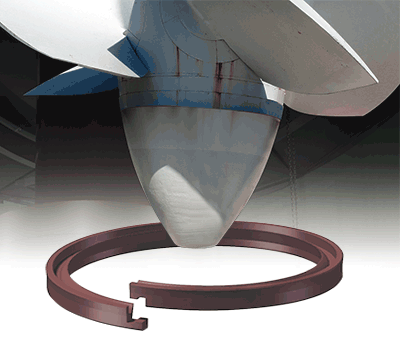
The Runner Blade Trunnion Seal is just one of the fully array of Kaplan Turbine product solutions available from Chesterton.
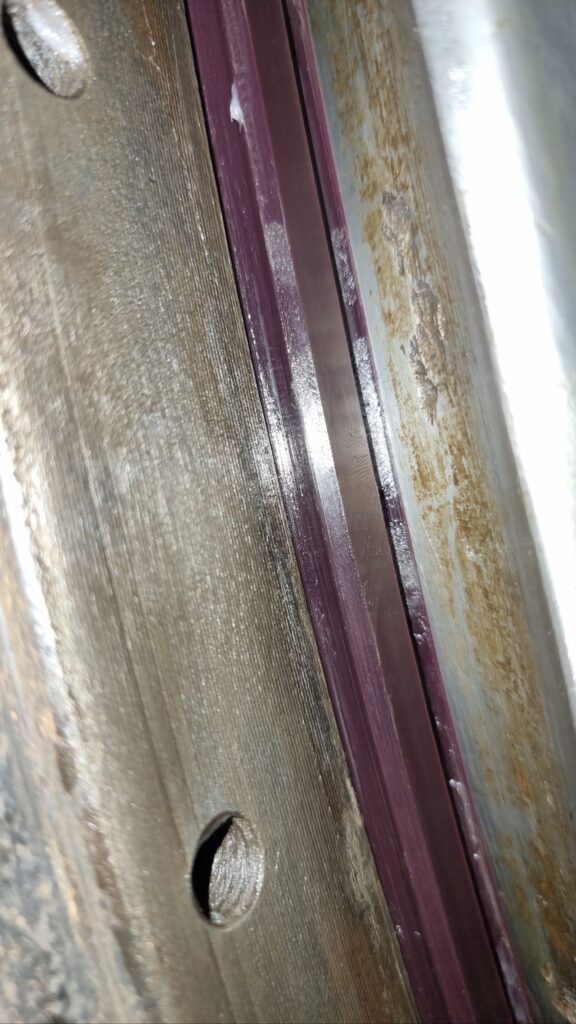
- Faster Installation & Increased Reliability
Because to its split design, the seal can be installed quickly and easily, reducing downtime. The removal of the blade is not required for installation and there is no need for complex welding, gluing, or post processing of the split joint. Furthermore, instead of requiring a complete stacked set, just two seals need to be installed back-to-back. This configuration also keeps the hydraulic media and lubricant in the turbine hub, and protects the hub against ingress of water, solid particles and sediments.
- Maintains Load Pressure & Rotary Shaft Movement
The positive, flared dynamic lip design of the Chesterton Kaplan Runner Blade Trunnion Seal prevents the split from being pulled apart by rotating motion and uses load pressure to join the cut ends. During blade positioning, Chesterton’s seal maintains load pressure and allows for rotary shaft movement with minimal frictional drag.
- Compensates for Blade Droop
A typical reliability issue with an older Kaplan Turbine is blade droop caused by worn trunnion bushings. The Chesterton trunnion seal design compensates by providing reliable sealing despite any droop.
- Durable Seal Material Offers Longer Life in Hydropower Environment
This seal is comprised of Chesterton’s AWC800 high-performance thermoset polymer material, which has a proven record of withstanding harsh operating conditions and provides exceptional abrasion resistance and durability. To reduce frictional drag, the polymer contains a built-in molybdenum disulfide lubricant. Because of its superior memory, the seal can automatically adjust and correct for radial cross-sectional differences caused by blade droop.
Conclusion
The Chesterton’s 22KN5 Double Acting Kaplan Runner Blade Seals in Split Interlock configuration are considered as the most user friendly and ease installation sealing solution by worldwide end users comparing to other seals as traditional rubber seals or hot welded modern polyurethanes. Optimized, smart and precise design of the 22KN5 seals combined with high performance thermoset polymer material technology provides sealing, which does not need any glue bonding, welding or vulcanization process on site, making installation simple, fast and secure.
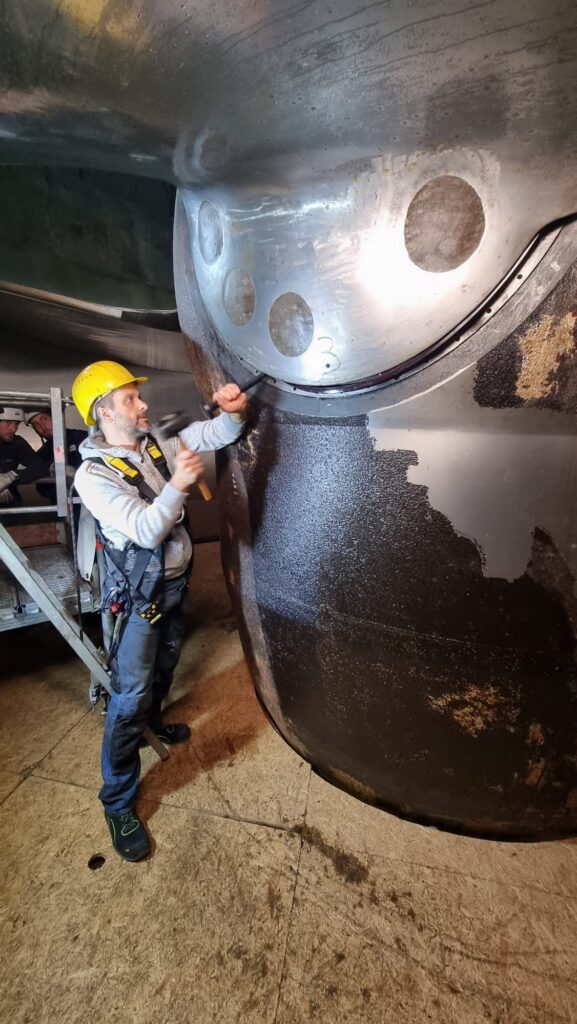
Do you have questions about our specific Kaplan turbine solution?
You can find more interesting details and information in our White Paper.
Please get more information about the mining applications of our sealing technology:
In our blog, we provide information on sealing Kaplan turbines and troubleshooting leaks
If you would like assistance selecting the best hydraulic seal solutions for your specific cylinder application, feel free to contact our Ask the Expert desk.
You can also make a preliminary selection using our product selector. Our product consultants will gladly assist you in selecting the ideal product for your application.