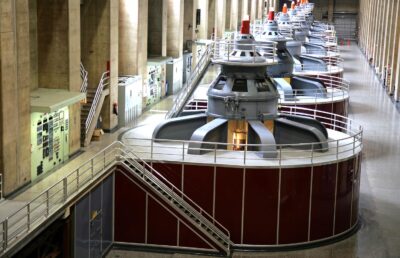
The hydropower industry faces the constant challenge of making its systems more efficient while maximizing the service life of components. In this quest for maximum performance and longevity, selecting the right sealing technology plays a crucial role. This article highlights the compelling benefits of Chesterton mechanical seals in hydropower plants and shows how this innovative technology can contribute to sustainable optimization.
Mechanical seals are critical components in hydropower plants, responsible for sealing pumps and turbines. Chesterton mechanical seals are characterized by their advanced design and material composition. These seals are specifically designed to withstand the extreme conditions found in hydroelectric environments while providing a reliable seal.
Many factors affect reliable turbine main shaft sealing. Shaft size, turbine speed, pressure, water sediment content, start-up conditions, cavitation vibration, and other factors will impact seal selection and the long-term success of the sealing device.
Large Turbines create Large Sealing Problems
One of the main challenges in hydropower plants is minimizing leakages in the turbines. Conventional main shaft turbine seals typically leak heavily and can cause considerable shaft damage. They also require clean, filtered water that is flushed within the seal to prevent solids from embedding between the sealing elements and the sleeve. The reliability and service life of your seal is directly dependent on the continuous operation of the filtration systems. They must be able to continuously supply filtered water to overcome seal leakage and pressure conditions.
The use of filtered water is extremely expensive. The stations’ drainage systems can overflow, which requires constant monitoring. The filter systems require regular maintenance, all of which leads to immensely high costs. In addition, the constantly flowing water causes severe corrosion damage to the metal parts.
Chesterton split seals are designed to seal leak-free. With our innovative technology and sealing materials, we can deliver superior sealing solutions that meet the dynamics of your operation and develop reliable, long-term solutions that significantly reduce filter water requirements.
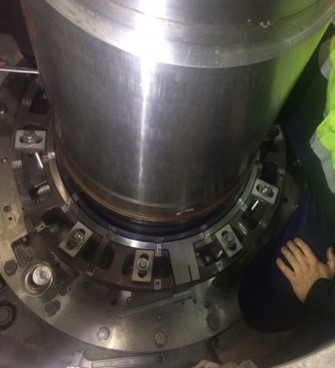
The Chesterton Solution for Reliable Sealing with Considerably Reduction of Flush Water
One of the biggest issues in developing a reliable seal solution for water turbines is keeping sediment and sand out of the seal so the particles don’t clog or wear out the seal or equipment. Based on our many years of experience in the hydropower sector, we have found an effective solution to this problem.
We combine our advanced split seals with SpiralTracTM technology to eliminate solids from the sealing environment and significantly reduce or eliminate the flush water requirements for turbine mainshaft seals. Controlling the adverse conditions under which the seal typically operates enhances the reliability of your sealing system and reduces operational costs.
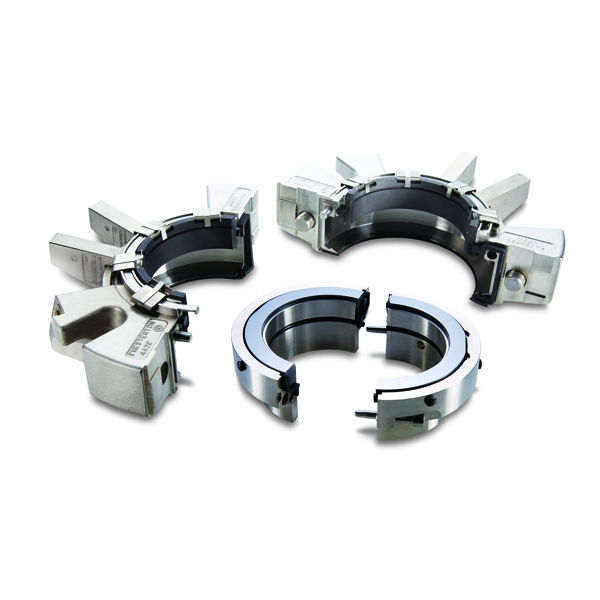
Chesterton’s innovative 442 split mechanical seals deliver a radically different level of sealing sophistication for hydropower plants around the globe.
A split seal has components split into two equal halves, which are secured as one unit on the seal shaft. The major advantage of the split seal design is that it allows you to install the seal with no dismantling of the pump (or equipment)—an enormous time-saver! Chesterton’s split seals offer virtually leak-free performance. This leads to improved safety and environmental compliance and nearly eliminates sleeve wear, and flush water usage, among many benefits.
Adaptability to different operating conditions
The versatility of Chesterton mechanical seals allows them to adapt to different operating conditions in hydropower plants. Whether the pressures are low or high, whether the plant is operated continuously or intermittently, these seals provide a reliable seal and thus contribute to the stability of the overall system.
Contribution to sustainable energy production
By reducing leakage, protecting against wear and adapting to different operating conditions, Chesterton mechanical seals make a significant contribution to sustainable energy production. The optimization of hydropower plants leads to increased efficiency and helps to minimize the environmental footprint of energy production.
Conclusion
The application of Chesterton mechanical seals in the hydropower industry is a pioneering step towards improving performance and reliability. The reduction of leakage, protection against wear and the adaptability of these seals make them a key component for the sustainable development of hydropower plants. At a time when the search for environmentally friendly and efficient energy sources is paramount, Chesterton mechanical seals are helping to cement hydropower as a viable solution for the future.
You can also make a preliminary selection using our product selector. Our product consultants will gladly assist you in selecting the ideal product for your application.