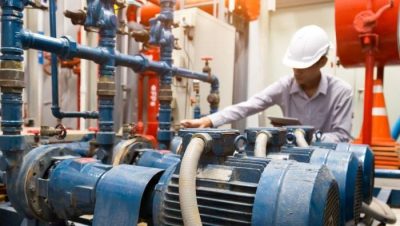
Vibration and surface temperature measurements are the most common methods of monitoring the condition of pumps and other rotating equipment. However, vibration and surface temperature measurements of the pump motor or bearing housing provide only half the story.
What are the main causes of vibration in pumps?
There are many sources of vibration in pumps. The most common causes are shaft distortion, imbalance, misalignment, reaction and contact forces between components. These problems can all affect the reliability and operation of rotating equipment.
An increase in vibration can lead to:
- Excessive shaft movement which eventually damages the seals
- Permanent indentations of the bearing races
- Deterioration of clearances such as those between bearings and wear rings
- Looseness
- Fatigue damage to components
Correlation of pump vibration monitoring with process pressure and temperature
When looking at a pump and the causes of pump failure, we need to look at all of its components more broadly. It is important to note that pump failures do not always start with changes in vibration and surface temperature. The failure conditions of some pumps start with pressure changes – which eventually result in vibration. Fluctuations in fluid characteristics, changes in speed or direction of rotation, obstructions at the discharge or suction end, and wear of internal components in contact with the fluid can all cause changes in pump pressure.
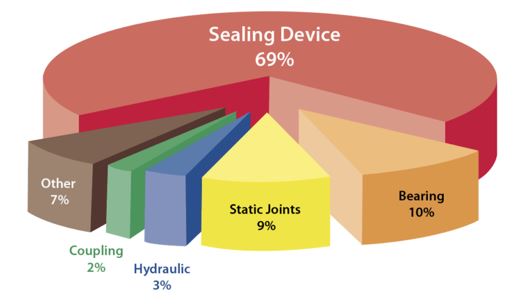
Pump failure point no. 1: dynamic seals
The first and most common component to fail in pumps is the dynamic seal.
Seal failures can be caused by multiple factors, many of which are not detected in the early stages.
Some of the most common factors are changes in pump suction and discharge pressure. These changes directly affect the pressure and temperature of the seal chamber (also known as the gland) – ultimately affecting the mechanical seal.
For example: during pump operation, the observation of an increase in vibration, followed by an increase in temperature and a drop in pressure of the pumped medium in the seal chamber is most likely caused by a restriction on the suction side of a pump.
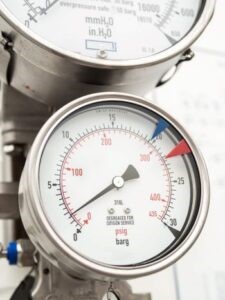
In this scenario, if only bearing vibrations and surface temperature are monitored, changes (pressure, temperature) inside the pump would go unnoticed. With an increase in temperature and a drop in pressure inside the seal, the sealing device (e.g. barrier fluid) could experience operating conditions similar to those observed during dry running, causing premature failure of the dynamic seal and ultimately pump failure.
For a double mechanical seal working with barrier fluid, monitoring the pressure and temperature of the barrier fluid reservoir and that of the pumped fluid inside the pump will confirm that we have the correct pressure differential to ensure proper lubrication and operation of the mechanical seal.
Monitoring the pressure and temperature of the pumped medium in conjunction with the vibrations can provide a clear understanding of the pump’s condition, helping the user to correct pump disturbances in advance and thus avoid failure and increase uptime.
Pump failure point 2: Bearing
Bearings are the second most common component to fail in pumps.
Typically, bearing failures are caused by corrosion due to seal leakage, equipment imbalance, shaft misalignment, damaged impeller, etc. Bearing maintenance is normally preventive. Bearings are often replaced on the pump during seal maintenance, even when they are still in good condition.
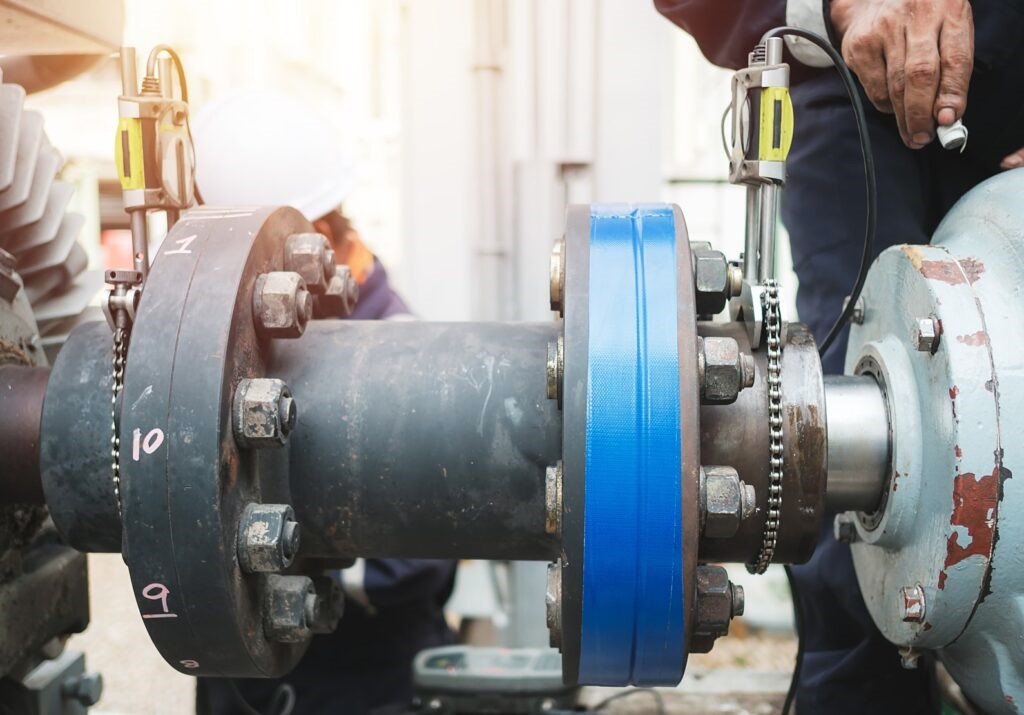
Full monitoring of pump conditions
In summary, pressure, temperature of the fluid being pumped and pump vibration must be monitored to truly provide a complete and accurate picture of a pump’s true condition. The Chesterton Connect ™ sensor, mobile app and Cloud analytics provide 24/7 visibility of an equipment’s condition in all four areas (process pressure, process temperature, vibration and surface temperature) to enable you to identify problems in advance and make corrections for overall increased reliability and improved plant performance.
The following are case studies demonstrating how the Chesterton Connect sensor has been used to monitor process pressure, temperature and vibration, providing essential information for achieving equipment savings.
Case Study 1: Identifying dry running conditions
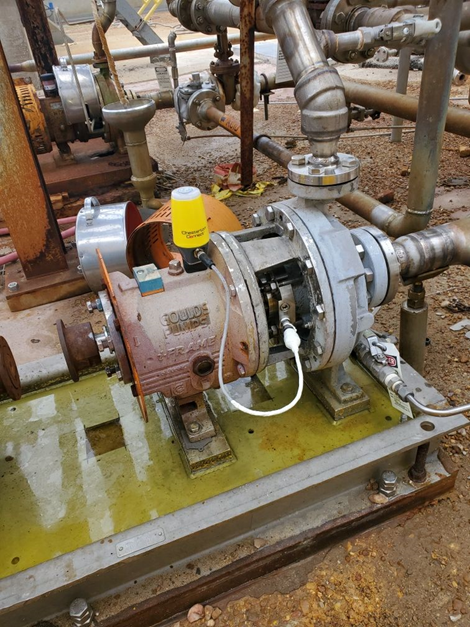
A chemical plant had an unusually high number of failures of single cartridge mechanical seals installed on a 65% nitric acid transfer pump. The mean time between repairs (MTBR) was only 1.2 months.
A technician checked the operation of the system and the installation of the mechanical seal and found no significant problems in the operation of the pump.
Our specialist recommended the installation of a Chesterton Connect. Within a few days they were able to quickly gather enough information to determine that there was negative pressure in the seal chamber when the pump was running. This negative pressure caused the mechanical seal to exhibit classic dry running symptoms. After conducting a system audit, the customer was able to push back a valve to ensure proper pump flow.
The pump and mechanical seal are now working properly and the projected MTBR has increased to over 24 months. The potential cost savings for the mechanical seals for this pump is over $30,000. Savings due to reduced maintenance and operational improvements are estimated to be even greater, but are still being calculated at this time.
Case study 2: Vertical multistage pump
A pump seal installed on a vertical two-stage pump failed after 2-3 days.
The seal was changed and again, 2-3 days later, the seal failure returned. Obviously there was a problem, but no one knew why, and it was impossible to “see inside” the mechanical seal to determine the root cause of the problem.
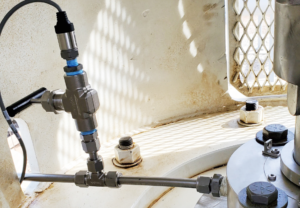
A Chesterton Connect ™ sensor was installed to monitor process conditions causing premature seal failure. Using the Chesterton Connect app, the user was able to plot the process pressure (falling) and temperature (rising) while the pump was running.
Using Chesterton Connect data, significant changes in the pump’s operating environment were identified and the seal failure problem was resolved.
Original article from JUAN CID
More information