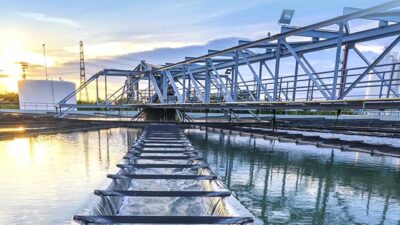
The water and wastewater industry is grappling with numerous challenges. Rising energy and maintenance costs, stringent environmental regulations, and aging infrastructure demand specific attention and solutions.
Pumps, mixers, and agitators in water and wastewater treatment facilities must operate continuously. The constant use and long service life of these machines place significant stress on all components. Chesterton mechanical seals have demonstrated their ability to lower maintenance costs and increase equipment uptime. Split mechanical seals, in particular, are designed to extend the life of worn equipment by upgrading from gland packing
Key Benefits of Chesterton Mechanical Seals
- 1. Enhanced Safety and Reduced Maintenance Costs: The Chesterton 442C split seal can be installed without disassembling large equipment, significantly reducing maintenance costs and enhancing safety. This innovation allows for quick and efficient seal installation, minimizing downtime and labor expenses.
- 2. Active Throat Bushing Technology for Water savings: Active throat bushing technology removes particles from the pump’s stuffing box, protecting mechanical seals and extending their life. The combination of a single SpiralTrac® and the Chesterton 442C split seal can significantly reduce, or in some applications, eliminate the need for flush water, further lowering operating costs.
- 3. Improved Efficiency reduces overall cost: High-quality sealing technologies are crucial for the efficiency of wastewater systems. The Chesterton 442C split mechanical seal enables seal installation without pump disassembly, saving valuable labor hours and minimizing downtime.
Split Seal Technology from Chesterton
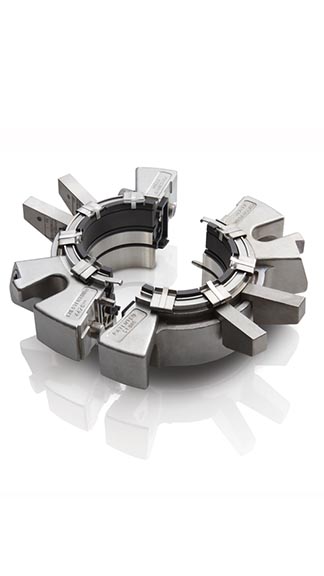
Split seals, as the name suggests, use split components that are mounted on the shaft. The Chesterton 442C Cartridge Split Seal offers superior sealing performance with easy and safe installation. This patented technology ensures reliable operation and long-term leakage protection for various rotating equipment, even under pressure-vacuum cycling and high-temperature conditions:
Lubricating the seal faces with clean fluids is essential for the longevity of mechanical seals. Traditionally, pump operators have used clean flush water to achieve this, which incurs significant water consumption and costs. Our advanced split seals, combined with SpiralTrac® technology, substantially reduce or eliminate the need for clean flush water, increasing the reliability of the sealing system and cutting operating expenses.
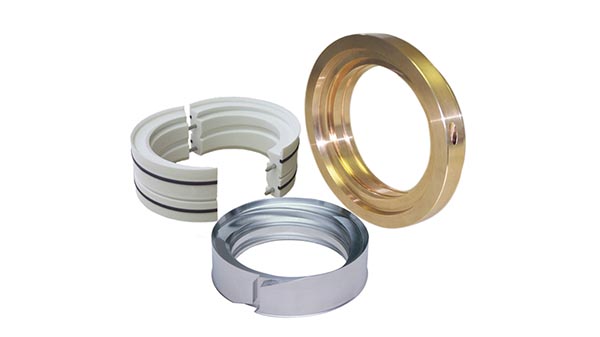
For more information about our mechanical seals, visit our “Reliability Matters” blog, which covers essential topics such as the “5-key Features for good Mechanical seal Design“
Here you can gain an insight into our decades of experience in the water and wastewater sector:
Case Study #1: Wastewater Plant Dramatically Reduces Seal Installation Time with Split Seals
Case Study #2: Reduce Flush Water Usage by 90% with Chesterton Split Seal 442
Case Study #3: Split Seals Deliver Reliable Wastewater Pump Sealing for Three Years Running
Case Study #4: Sealing Large Influent Pumps – Split Seals Increased MTBF to 9+ Years
Case Study #5: Chesterton 442C Cartridge Split Seals Switch Results in Easy Installations
Conclusion:
The water and wastewater industry faces numerous challenges, from ensuring safety and managing aging infrastructure to reducing energy consumption and maintenance costs. Advanced mechanical sealing solutions, particularly split seals, offer a practical and effective way to address these challenges. As the industry continues to evolve, the adoption of such innovative technologies will be crucial in achieving sustainable and reliable water and wastewater management.
Do you have any questions about our Mechanical Seal Technology? Our Expert Desk is here to help. We are happy to assist you!
You can also make a preliminary selection using our product selector. Our product consultants will gladly assist you in selecting the ideal product for your application.
*SpiralTrac® is a trademark of EnviroSeal Engineering Products Ltd.