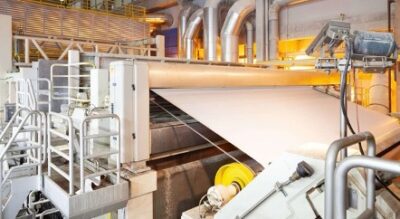
Paper and pulp production is an extremely demanding industry. It is a long way from the processing of raw wood to the production of fine writing paper. In many manufacturing steps, the abrasive raw material is processed with hot water and chemicals. This means that all machine components need to be highly resistant to wear, high and changing temperatures and chemical attack.
A wide range of pumps and rotating machines are used in this industry. Digesters, mixers, agitators, pulp pumps, screw conveyors, steam boilers – all of this equipment requires high-performance pump packing or shaft seals for efficient operation. Failures of individual pumps and machines can affect the entire process chain and can be very expensive if not addressed in a timely manner.
The use of innovative sealing technologies can increase the service life of the equipment and significantly reduce maintenance costs. Flushing water consumption is also considerably reduced, which is also a major benefit for the environment.
Chesterton offers High-Performance Packing for Demanding Applications
Reduced leakage, reduced maintenance, longer machine life – you can achieve these benefits by choosing the right mechanical packing.
Our extensive portfolio includes high quality packing solutions that can provide excellent sealing performance, reduce operating costs and increase the productivity of your equipment by reducing downtime. We would like to highlight some special products for the complex paper industry:
Chesterton® 377 CarbMax™ packing is successfully used for very demanding rotating machines, such as digester applications in the PPI sector. Braided to a high density, the product offers high resistance to abrasive materials and chemicals. The Chesterton 377 CarbMax™ packing is characterized by good thermal conductivity; dissipating frictional heat from the dynamic sealing surface. This robust design ensures a long service life of the packing with low maintenance requirements. This shaft seal can improve the overall efficiency of your system by significantly extending the Mean Time between Repairs (MTBR).
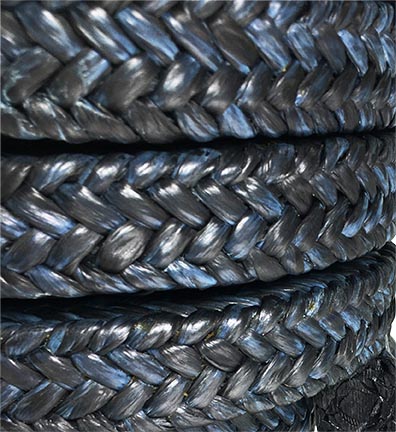
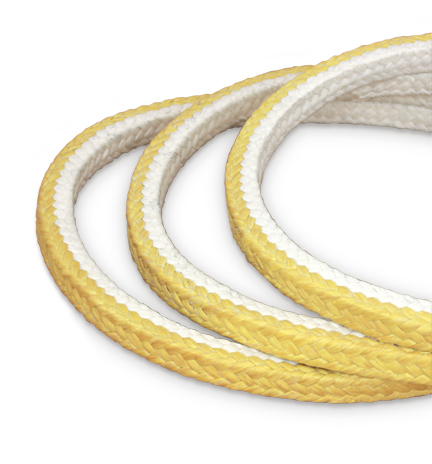
The Chesterton DualPac® 2212 packing is a temperature-resistant, non-staining, high-pressure packing with superior sealing performance that requires minimal gland adjustment.
Thanks to the patented braiding process, the DualPac 2212 packing combines burn- and glazing resistant materials on the shaft side with high-strength fibers on the outside.
The high strength aramid fibers on the outside give the packing a strong, extrusion resistant and resilient base. The dynamic shaft side of the packing remains firmly pressed against the shaft and helps to ensure that the stuffing box requires only minimal adjustment, that leakage is reduced, and that the shaft is not damaged by burning and scoring.
Many fluid media contain particles – such as the paper pulp in the pulp and paper industry. The problem with solids is that they cause excessive wear of the shaft sleeves and reduce the life of the packing. The solids usually settle at the interface between the rotating shaft sleeve and the pressure packing as they pass through the stuffing box. This reduces the Mean Time Between Repairs (MTBR) and increases maintenance costs.
In addition to our high quality stuffing box packings, we recommend SpiralTracTM technology* to remove solids from the sealing environment to prevent wear of the shaft sleeve.
Advantages of the additional use of the SpiralTracTM packing device
- Reduction in pump and rotating machine downtime
- Extension of the service life of pumps and rotating machines
- Increased service life of the stuffing box packings used
- Extension of the MTBR
- Reduction in the amount of flush water required (often by 60% or more)
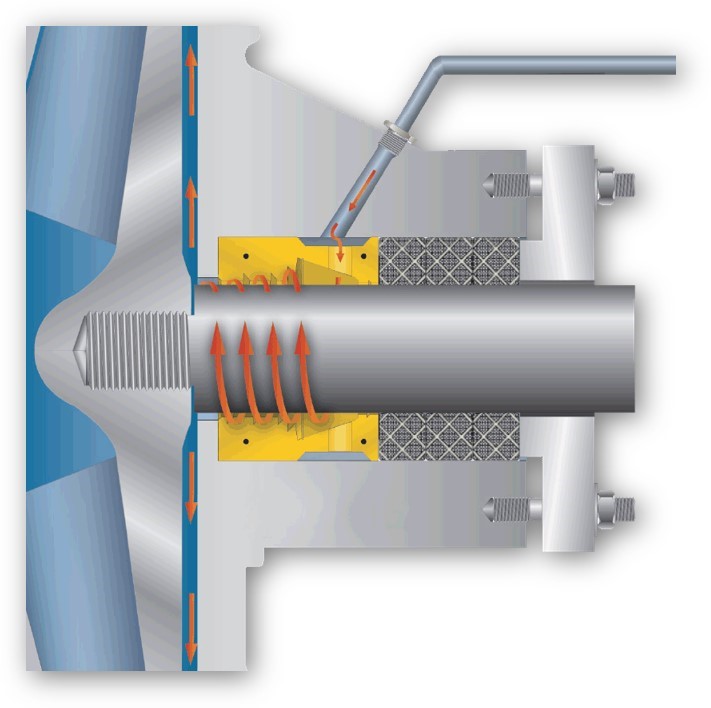
When stuffing box gland bolts are difficult to access, manually adjusting the packing can be difficult and put the safety of personnel at risk.
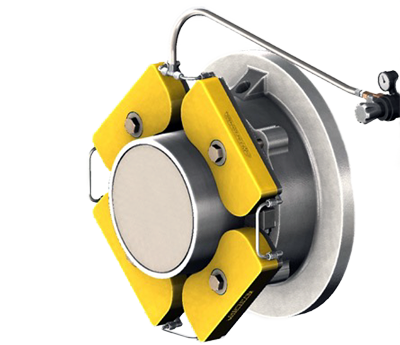
This is where our Chesterton AMPS™ (Automated Mechanical Packing System) innovation is the solution. By automatically adjusting packing compression, this technology significantly reduces maintenance costs and eliminates any safety concerns. The AMPS unit maintains a constant force to the packing at all times. This process, called Active Loading, provides an even and consistent load that eliminates the need for manual packing adjustments and maximizes packing performance and life. This technology helps to minimize leakage, reduce maintenance and improve sealing performance. It also increases operator safety by allowing remote adjustment of the stuffing box pressure.
Here you can gain an insight into our valuable experience: (case studies from www.chesterton.com)
Case Study #1: Reduce Maintenance Costs and Increase MTBR for Sorting Screw Conveyor
Case Study #2: Increase MTBR on Oxygen Reactors with 377 CarbMaxTM Packing
Case Study #3: Paper Mill Improves Equipment Reliability and Safety with Chesterton® Solutions
Conclusion
Chesterton offers high performance packing products combined with new technical and automated innovations, which can significantly reduce the operating and maintenance costs of your rotating equipment, significantly extend MTBR, and clearly reduce leakage and shaft wear. Together with the advanced Chesterton mechanical seals, you get complete, plant-wide shaft sealing solutions.
We will gladly help you with any questions regarding Chesterton Mechanical Packing Devices.
Please ask our Expert Desk for further information.
You can also make a preliminary selection using our product selector. Our product consultants will gladly assist you in selecting the ideal product for your application.
*SpiralTracTM is a trademark of EnviroSeal Engineering Products Ltd.