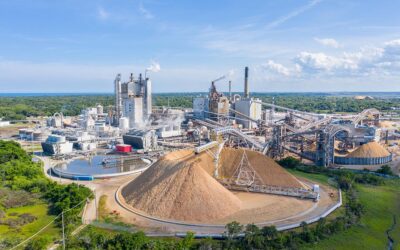
The pulp and paper sector is a demanding industry. From debarking and wood processing to the chemical processing of paper pulp and the manufacture of finished products – the work steps in this field are complex. The production of paper, cardboard and pulp requires many machines, a lot of water and certain chemicals. Plant operators have major challenges with corrosion and abrasion, which can affect the plants’ operation and performance. Increasing equipment performance, occupational and environmental safety and energy saving are extremely important for manufacturers to be able to reduce costs and increase profitability.
How can Chesterton help to improve efficiency in pulp and paper production with high-performance industrial coatings?
The processes used in the production of pulp and paper from wood chips, recycled paper and fibers are associated with high temperatures, high pressures, wear, abrasion, impacts or corrosion, all of which can affect the operation of mechanical equipment in various parts of the plant. High costs are incurred due to the wear of metal and concrete surfaces, erosion or cavitation of pumps, or corrosion caused by contact with chemicals. With Chesterton coatings, not only can new equipment be protected to increase the meantime between repair or failure, but also the repair and reconstruction of already damaged components is possible to increase operating lifetime, reduce spare part inventories and can therefore be extremely cost-efficient.
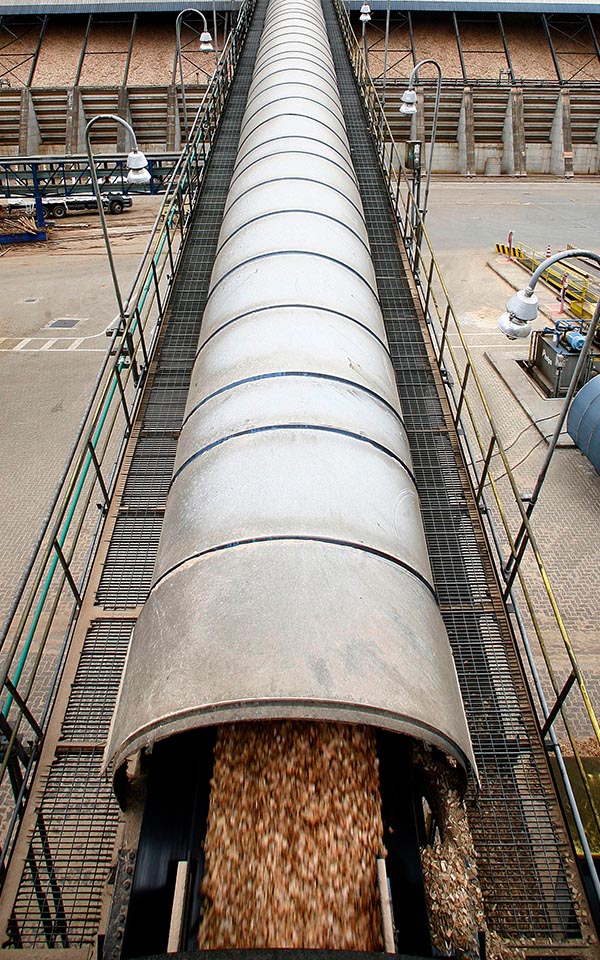
As in any other industry, the pulp and paper sector has several main targets:
- Increasing profitability and reliability
Chesterton offers a comprehensive portfolio of ARC and Ceramic-Polymer Coatings specifically designed for areas where severe abrasion resistance, long-term corrosion protection even in wet chemical applications or high temperature corrosion resistance are required. Whether concrete or steel substrates, the use of Chesterton coatings – also for surface repairs – can help extendthe service life of mechanical equipment. - Worker safety and environmental protection
The long-term performance of Chesterton industrial coatings significantly reduces the need for repair and maintenance work. This not only saves labor costs, but also increases the safety of personnel. The environment benefits, for example, from properly coated secondary containment basins that prevent chemical-containing production water from entering the surrounding area. Repair and protection of operating equipment with Chesterton coatings also contributes to improved environmental performance by reducing the number of new parts that must be kept in inventory. - Energy saving
The application of smooth high performance ceramic coatings to fluid flow equipment such as agitator propellers, cyclones, pipes, and many types of pumps can increase the flow speed of the fluids being handled, reduce power consumption, increase machine efficiency, and thus contribute to energy savings.
Benefit from our experience in the pulp and paper industry
Debarking Drums, Log Conveyors and Chippers, Agitators, Cyclones, Fan and Vacuum Pumps, Screws, Pulp Tanks, Press Rolls as well as Wastewater Tanks and Barrier Tanks – all these types of equipment can benefit from increased abrasion and corrosion protection. Chesterton industrial coatings of the ARC and Ceramic-Polymer product lines contribute to a considerably increased service life of the machines and the profitability of the entire plant is significantly improved. Furthermore, unscheduled machine downtimes due to unexpected failure or damage can be effectively prevented.
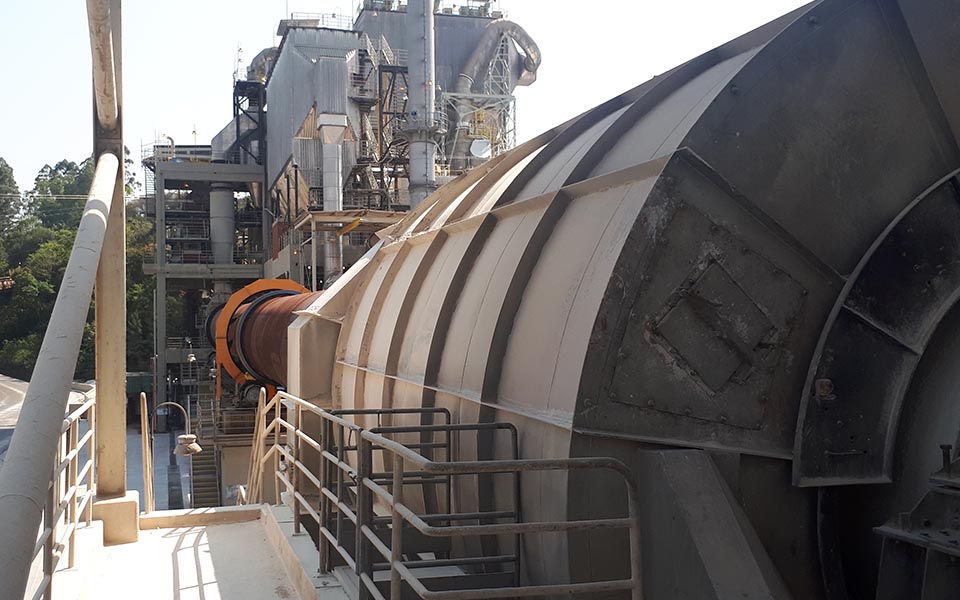
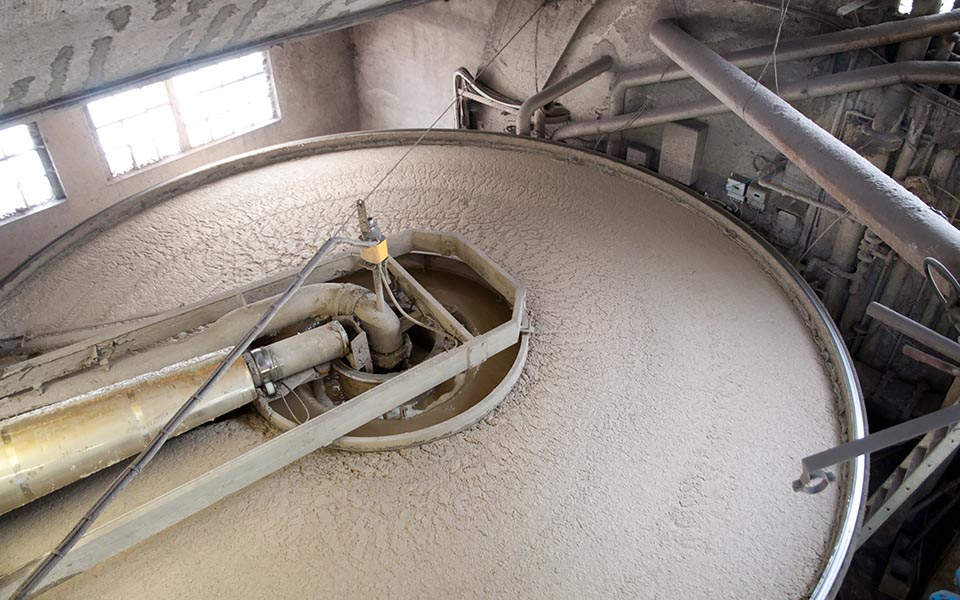
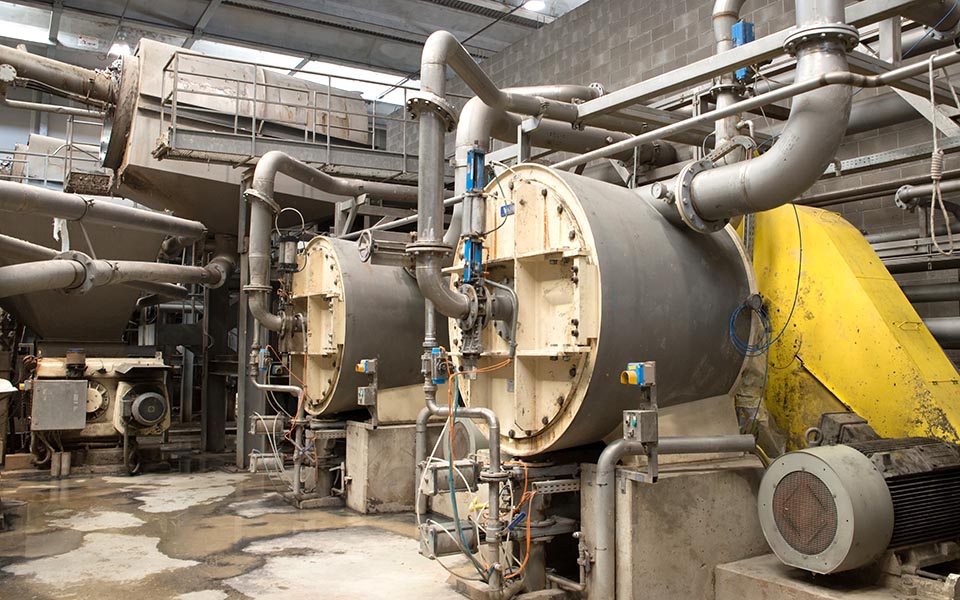
The high-performance Chesterton coatings provide long-term protection for metal and concrete surfaces with the following properties:
- 100% solids
No evaporating solvents, enhances the safe use
Resists corrosion and permeation. - Maximum Adhesive Strength to Substrate
Resists disbondment, provide long-term performance. - Resists Underfilm Corrosion
Enables localized repair on small areas. - Manufactured Under Vacuum
Resists permeation through coating – critical for immersion applications. - Ceramic and Special Particle Reinforcements
Resists abrasion, extends equipment life, reduces spare parts, reduces downtime. - Abrasion, Erosion/Corrosion, Chemical, Temperature Resistance
Provides long-term protection of metal or concrete surfaces. - Cost effective
Versus traditional repair methods. - Ease of application
1-layer application by hand tools or airless spraying, saves working time and can often be applied on-site without removal of equipment. - Cold curing Technology
No hot work or welding is required.
From wood to paper – requirements for coatings to protect the mechanical equipment
First, the bark is removed from the logs, and they are processed into wood chips. Debarking Drums and Screws Conveyors or Chutes require coatings that are highly resistant to impact and abrasion.
Our ARC I BX1(E), for example, is designed precisely for such demanding operating conditions. High impact resistance, hardness, and resistance to sliding wear characterize this product, hence it is also used in the mining sector.
The ARC BX2(E) is equipped with finer particles and is applied for areas in pulp processing, such as screw presses and agitators, which require moderate abrasion resistance but increased temperature resistance and chemical resistance.
The thick film coating ARC 858(E) is ideally suited for rebuilding heavily corroded or eroded metal surfaces in pumps or pulp tanks. ARC 855(E) and ARC SD4i(E) are often used as a topcoat for these repaired surfaces. With a thin layer, this system protects metal substrates against abrasion, erosion corrosion and chemical attack.
Of course, the Chesterton portfolio also includes coatings for the protection of concrete structures, such as wastewater basins, stock, pulp and whitewater chests or secondary containment areas with chemical tanks.
Talk to us! We will be happy to offer you the optimum coating solution. Please ask our Expert Desk for further information.
You can also make a preliminary selection using our product selector. Our product consultants will gladly assist you in selecting the ideal product for your application.