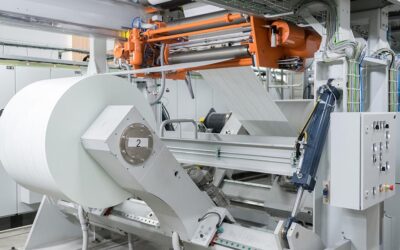
The pulp and paper industry uses complex paper machines that run 24/7. As in every industry, efficiency is also the key word for this sector. The goal is to achieve a high level of reliability for machine components and significantly reduce downtime for equipment repairs. With the suitable polymer seals for the various machine components, Chesterton can help to effectively extend the operational reliability and MTBF (Mean Time Before Failure).
Paper machines consist of a variety of equipment, ranging from rotating equipment of all kinds to hydraulic and pneumatic cylinders, hydraulic directional valves, control automation, but also various types of fittings such as valve flanges and dispensing systems. Chesterton offers specific polymer seals made from high-performance materials for these different devices.
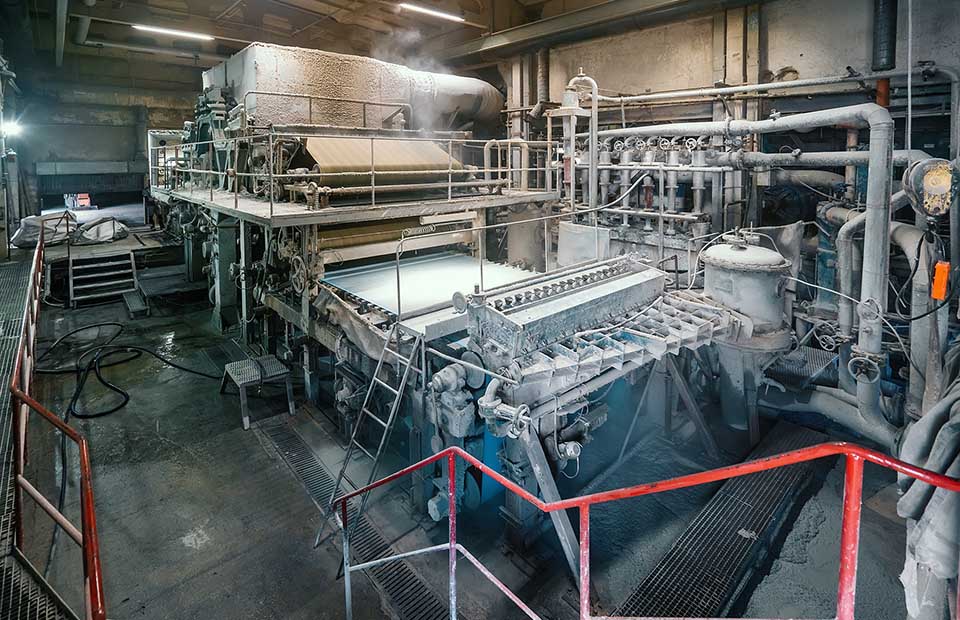
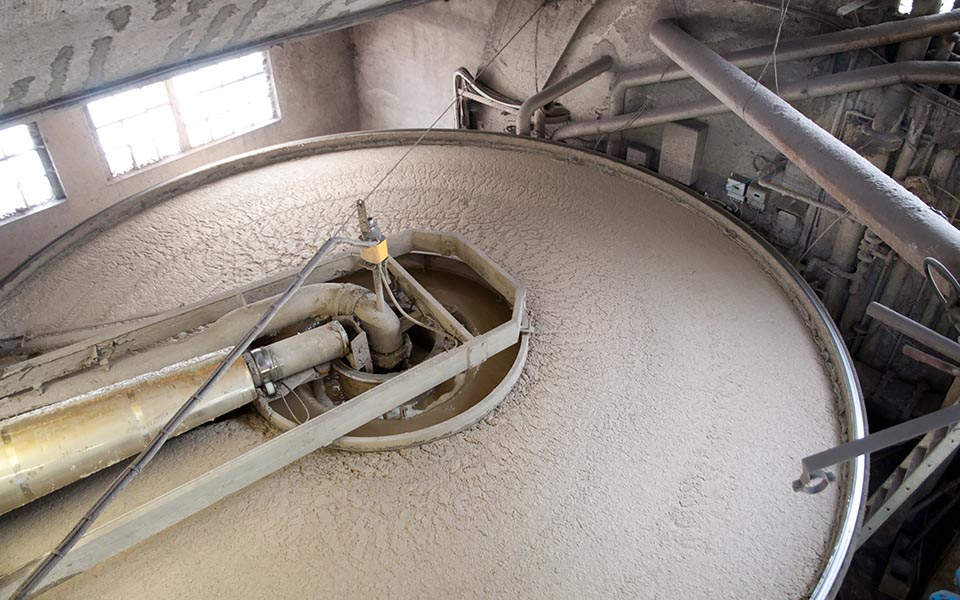
Rotating equipment in the paper industry: What are the challenges and how can we counteract them?
In rotating machinery such as pumps, agitators, hydropulpers, gearboxes, fans, bearing housings, electric motors, and roll pivots, bearing failure is the main challenge. In the tough world of the pulp and paper industry, bearings are exposed to a variety of contamination including water, dust, heavy loads, vibration, abrasive contaminants and corrosive vapors. This leads to unreliability and very often to a significantly shorter bearing life.
Bearings usually have lip seals (usually made of some kind of elastomer such as rubber) as a first line of defense. However, these only protect the bearing for a short time, far below the actual bearing service life. The rubber lip seal is there for keeping lubricant such as oil or grease inside the bearing not as protection function and was not designed for it even in many cases.
If these conventional lip seals fail, liquid from the environment penetrates into the bearing housing. This washes away the second line of defense – the grease – and exposes the bearing metal to the extremely corrosive atmosphere. Heat, chemical load and the humid ambient conditions lead to bearing corrosion. Due to corrosion, bearings fail after a few thousand operating hours and, in the worst case, to the failure of the entire machinery. The solution to premature bearing failure is, of course, a high-quality grease for smooth bearing movement and a functioning lip seal. This can significantly extend the MTBF (Mean Time Before Failure) and the bearing service life.
The first line of defense for equipment storage – Chesterton® Rotary Seals

Chesterton has an extensive portfolio of excellent rotary seals, in particular the 30K Bearing and Gearbox Protection Seal, which is often chosen in the paper industry for its outstanding protective properties and durability.
Furthermore, the split polymer seals are explicitly suitable for rotating equipment in the paper industry, offering high performance and quick and easy installation. For example, Chesterton’s patented Matrix Rotary Seal is a split bearing protection seal developed to work on worn shafts and applications with high shaft runout.
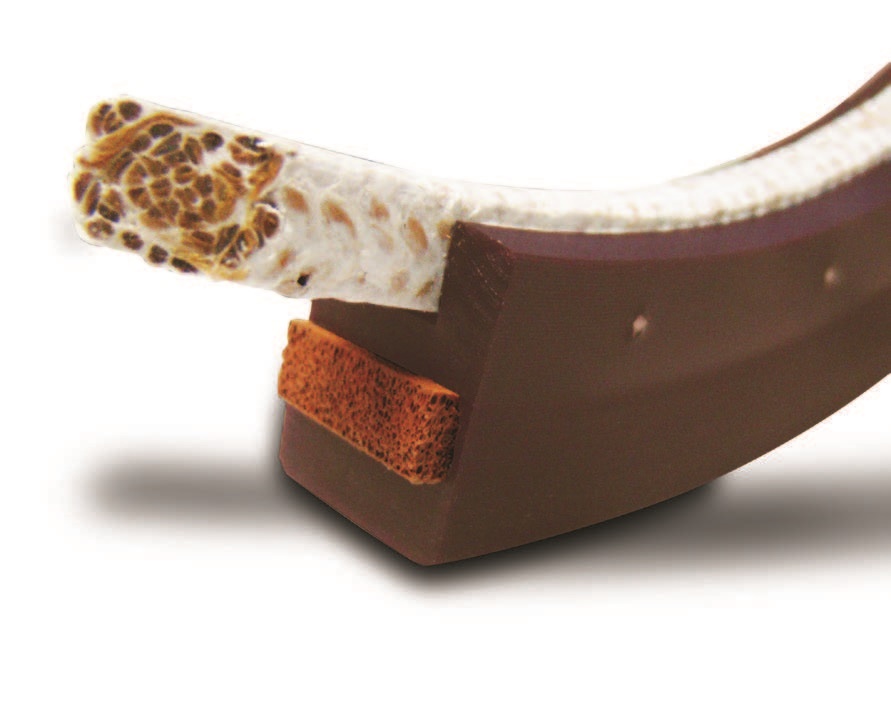
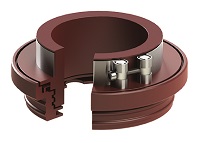
The non-contact Split Polymer Labyrinth Seal (SPLS) is specially developed for splash water lubricated bearing protection in large pumps, gearboxes and other rotating equipment. Here, the specific design helps to ensure effective protection: during operation, centrifugal forces and gravity ensure that the lubricant remains in the labyrinth and flows back into the bearing housing, while contamination from outside is excluded and directed back into the atmosphere.
The R22KN5 Split Rotary Seal is used for slow-rotating applications. There are high-performance polymer materials, such as AWC860 Cherry Polymer, which are one of the best sealing solutions for pulp washer screens and filters in cellulose production.
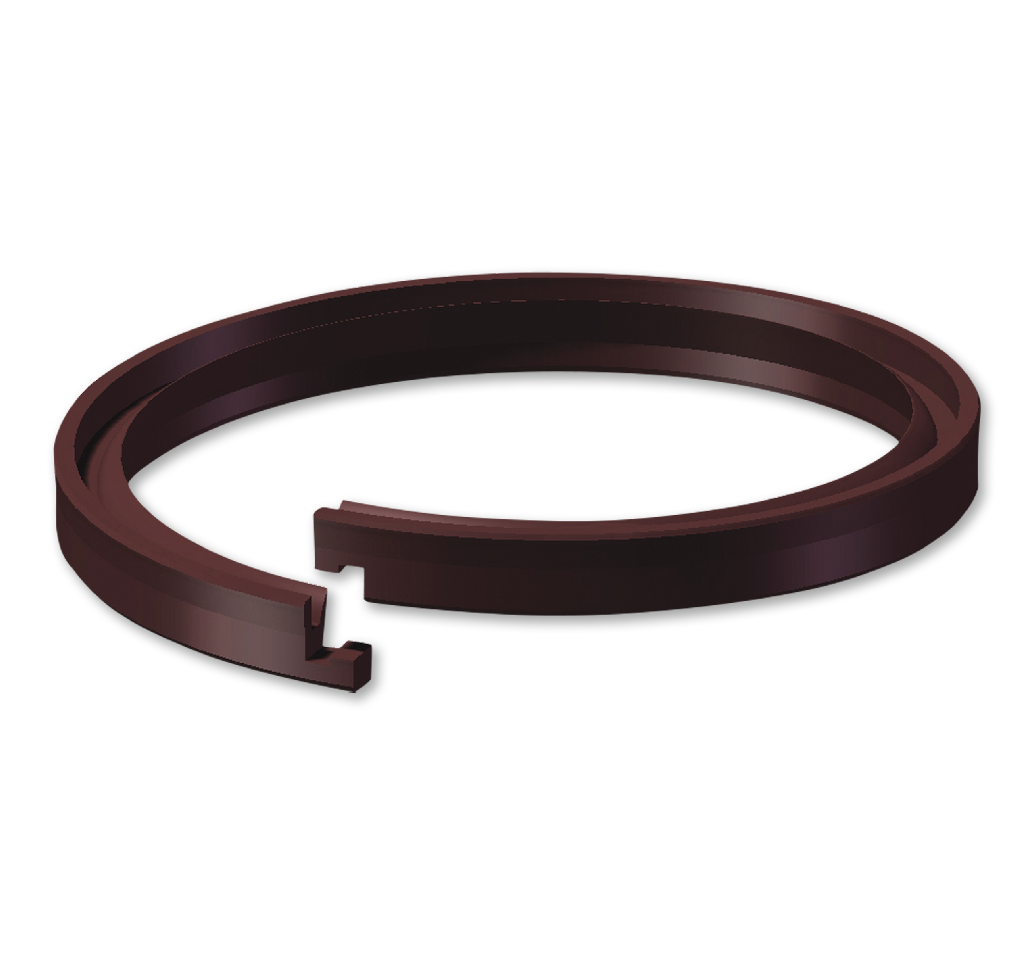
Product advantages and product benefits of Chesterton polymer seals for the protection of machine bearings
- Low shaft friction
- Sealing against external contamination of the bearing
- Maintaining bearing lubrication
- Long service life
- High-performance construction and material
- Simple installation (with split seals)
- Extending the MTBF of rotating equipment
Cylinder optimization with the 1-2-3 System from Chesterton – extending the service life of hydraulic cylinders
In the pulp and paper industry, there are numerous hydraulic devices such as cylinders, presses, lifters, valve drives, pumps, control valves and directional valves. If cylinder seals do not perform adequately, leaks occur and hydraulic fluids spill out. These leakages cause contamination of the product, which leads to production losses, and have a negative impact on the environment and occupational safety.
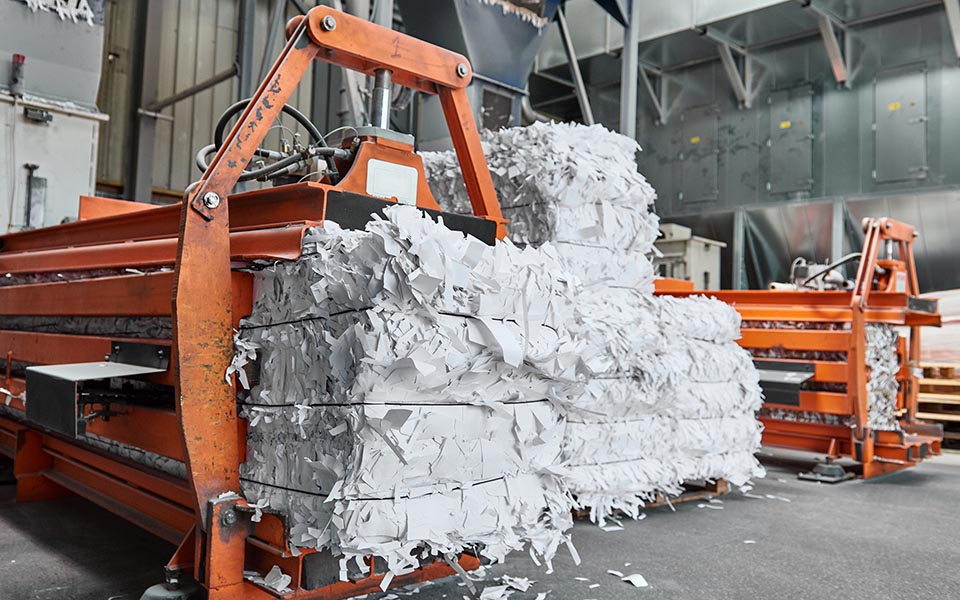
Defective seals also provide no protection against external influences and contamination. Dirt particles enter the cylinder, causing corrosion and failure of the hydraulic system.
Product-specific designs and complete sealing kits for cylinder applications optimize the performance of your systems. Complex packages for engineering advice, on-site support, failure analysis and retrofit components are also included in the comprehensive Chesterton service.
The use of our high-performance cylinder seals in application-specific materials can
- Minimize downtimes and maintenance costs
- Improve reliability of the hydraulic system
- Help extend the service life of hydraulic cylinders
- Reduce the consumption of hydraulic fluid, avoid leakages
- Significantly reduce operating costs and achieve considerable savings
Benefit from our experience – here you can gain an insight into our field of activity:
Case Study APAC0032 – Pulp and Paper – Polymer Labyrinth Seal
Case Study APAC0038 – Pulp and Paper, OEM lip seal – Polymer Labyrinth Seal
Conclusion
Chesterton’s advanced polymer seals increase the reliability of rotating and hydraulic equipment in all sort of Pulp and Paper plants. They help to protect bearings and hydraulic systems from wear and abrasion, enabling a longer service life for mechanical equipment. Our special polymer materials with excellent mechanical properties contribute to the efficiency of your equipment, even in the most demanding applications. Our unique split sealing solutions offer technically superior sealing and savings of thousands maintenance hours. Discover the comprehensive Chesterton portfolio.
If you have any technical questions or if you would like assistance selecting the best sealing solutions for your specific pulp and paper application, please feel free to contact our Ask the Expert desk.
You can also make a preliminary selection using our product selector. Our product consultants will gladly assist you in selecting the ideal product for your application.