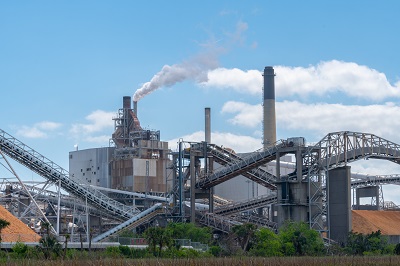
Modern paper machines are up to 150 meters long, 10 meters wide and run at speeds of up to 2000 meters per minute. Huge giants, 24/7 in operation, programmed for smooth production without downtime. Outside of the paper machine itself there is a complex process including the wood yard, stock preparation, pulping and paper conversion.
The operational challenges of the pulp and paper industry are complex. The production process is demanding, and equipment is constantly exposed to a humid and chemical-laden atmosphere. Without suitable lubricants, damage occurs to rotating machinery, which in the worst case can bring the entire plant to a shutdown and result in extremely high maintenance costs. Maximizing the Mean Time Between Failures (MTBF) is essential to optimize the production process and profitability.
Defying all challenges – Chesterton® Advanced bearing lubrication
Lubricants are required to deliver top performance in the pulp and paper industry, as they have to perform reliably under harsh environmental conditions such as moisture, dust, contamination, chemicals, temperature, pressure or vibration. In these aggressive conditions, high performance lubricants and maintenance products help to keep machines running reliably and trouble-free, prevent premature equipment failure and thus increase plant productivity.
For these demanding applications, Chesterton provides lubrication products for chains, bearings, wire ropes, cables, open gears, pneumatics and sliding lubrication.
In this article, we focus on bearing lubrication, which plays a crucial role in the pulp and paper industry.
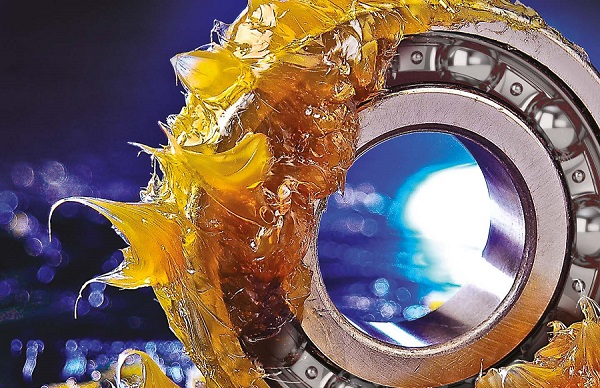
As a lubricant manufacturer, what special factors do we consider when developing bearing lubricants? What special benefits do our products offer paper mills?
- “Water and moisture” factor in paper mills – risk of bearing corrosion and wear
Conventional elastomer lip seals for equipment bearings are designed to prevent the ingress of water and moisture. However, their service life is limited, and reliable sealing diminishes after approx. 3000 operating hours. If these simple lip seals fail, water from the environment ingresses into the bearing housing and the grease can be washed away. Grease being washed away is a concern, but even more concerning is, with what it is replaced with, water!!!
Constant lubrication is now interrupted and bearing wear is accelerated by friction and corrosion. This reduces the service life of the bearing and leads to premature failure. Chesterton’s advanced sulfonate complex technology shows best in class water washout resistance and corrosion protection. This high performance can be seen in tests according to ASTM, ISO and DIN standards. You can find the test results on our product data sheets – feel free to compare them with those of our competitors. - “Load and vibration” factor – risk of bearing damage
Bearings are among the most important components of rotating equipment and electric motors. High speeds, heavy loads, high operating temperatures, start/stop function, high vibrations in rotating equipment – all these factors push bearings to their limits. Many customers replace the bearings on their equipment due to damage caused by wear and vibration. Chesterton lubricant technology contains advanced lubricity and extreme pressure additives that enhance grease performance in these challenging conditions for both, equipment and electric motor bearings. As with the “water/moisture factor”, there are standard ASTM, ISO and DIN tests to measure the performance of greases to help customers select the best product for their application. - The “human” factor in paper mills
Another factor that has not been addressed yet is the “human factor”. Timely manual lubrication often is not carried out consistently or regularly during the operational process. This can lead to over- or under-lubrication. Over-lubrication means excessive consumption of lubricants, is therefore uneconomical and can cause temperature build up, which reduces the lifetime of the grease and can lead to premature failure of the bearing. Under-lubrication can lead to system failure in the long term. Automatic programmable lubrication systems for grease and oil, such as the Chesterton Lubri-Cup™ dispenser, help ensure a regular and timely supply of lubricants.
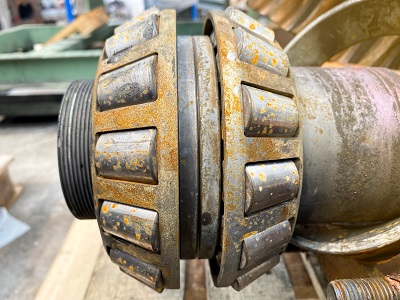
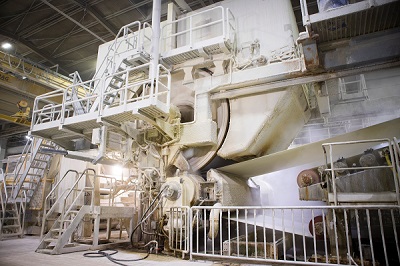
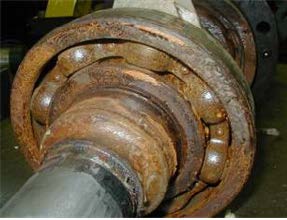
Continuous lubrication with Chesterton Lubri-Cup™ Lubricant Dispenser means optimum bearing performance and increased work safety
Our Chesterton Grease Lubri-Cup automatic lubricator provides the right amount of lubricant when required. It helps extend bearing lifetime and reduces bearing maintenance. As the name suggests, lubrication runs automatically with the right grease, at a constant interval with the correct amount of lubricant. Our “Stories of Success” result in longer service life of the bearings and an immense extension of the MTBF.
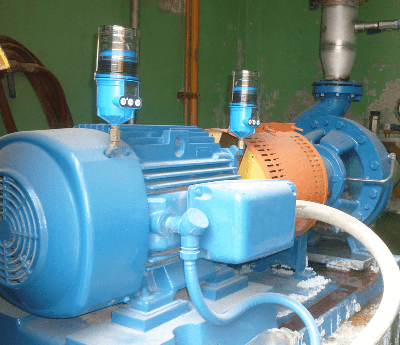
Here is one of our success stories:
“Our Lubri-Cups were used in a plant with over 7000 electric motors. The customer had a vibration monitoring program in place but found that some critical motors were experiencing excessive vibration causing premature bearing failure. The customer decided to run a test using Chesterton 638 Electric Motor Grease. Immediately after applying 638 EMG into the bearing housing, a reduction in vibration was visible. As a result of the test, the customer decided to use Chesterton 638 EMG as the standard grease for all electric motors. Other benefits for the customer included reducedgrease consumption and an increase in bearing lifetime. One of the reasons for the success of the 638 EMG was due to its additive plating technology called QBT (Quiet Bearing Technology). This helps fill any surfaceirregularities or damage on the bearing surface and allows the bearing to run more smoothly and quietly.“
Chesterton® High-Performance-Grease for bearing lubrication under extreme conditions
From our extensive portfolio of industrial lubricants, we focus on our high-performance greases 615, 617(E) and 638 EMG for the pulp and paper industry. These greases are specifically designed for heavy loads and high temperature applications in wet, corrosive environments. They are used in various equipment in many industries and offer outstanding performance for the lubrication of machine bearings.
Benefits include:
- Less grease washout, therefore lower grease consumption and lower acquisition costs. Elimination of bearing failures due to corrosion.
- High lubricity, extreme pressure performance – resulting in longer bearing lifetime and reduced downtime.
- Thermal and shear stability – elimination of oil bleed from grease and hardening in the bearing.
Bearing protection at its best – our lubricants and polymer seals
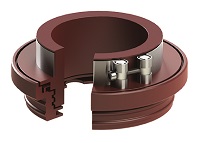
Chesterton also offers advanced bearing sealing solutions in the form of our Polymer Labyrinth Seal (PLS), which provides protection for the bearing and offers customers a significant advantage over conventional lip seals in terms of service life. In addition, this solution is available in a split design, which allows for easy installation.
Conclusion
The pulp and paper industry has very special requirements for machine bearings. The advanced lubricants from Chesterton help against “bearing killer” conditions such as corrosion, grease washout, load and vibration and make a considerable contribution to a long bearing life.
If you would like more information about our bearing reliability program, please contact our Expert Desk.
You can also make a preliminary product selection using our product selector. Our product consultants will gladly assist you in selecting the ideal product for your application.