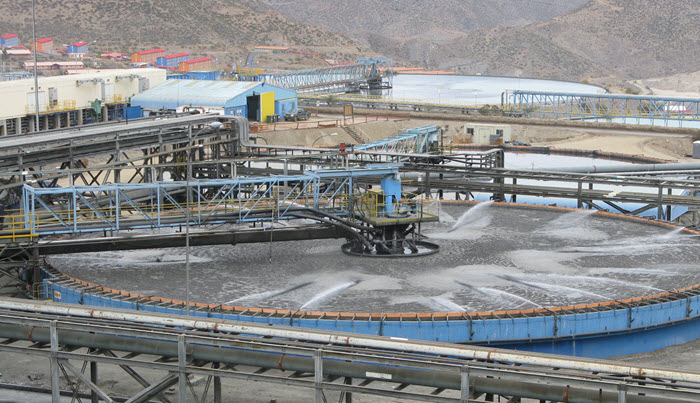
Slurry pumps are integral to many mining operations, but their maintenance, particularly the replacement of seals, can be challenging. The abrasive nature of slurries can wear down packing or clog mechanical seal components, reducing seal life to mere weeks or even days. With downtime proving costly, choosing an efficient and easily replaceable sealing solution is crucial.
Expedite Seal Replacement with Best Practices
In this article, we will discuss some best practices that can accelerate the process of replacing packing and seals in slurry pump applications.
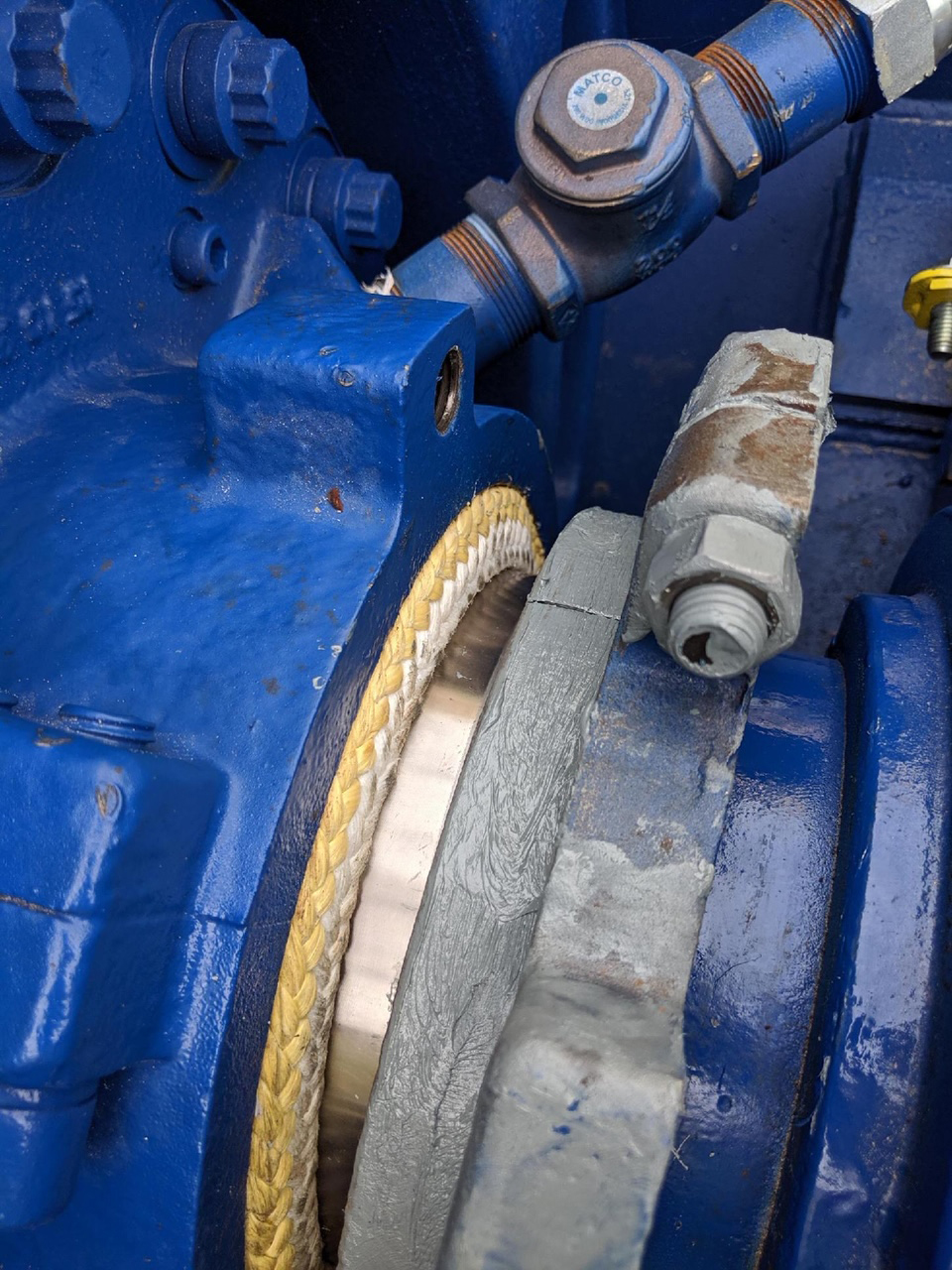
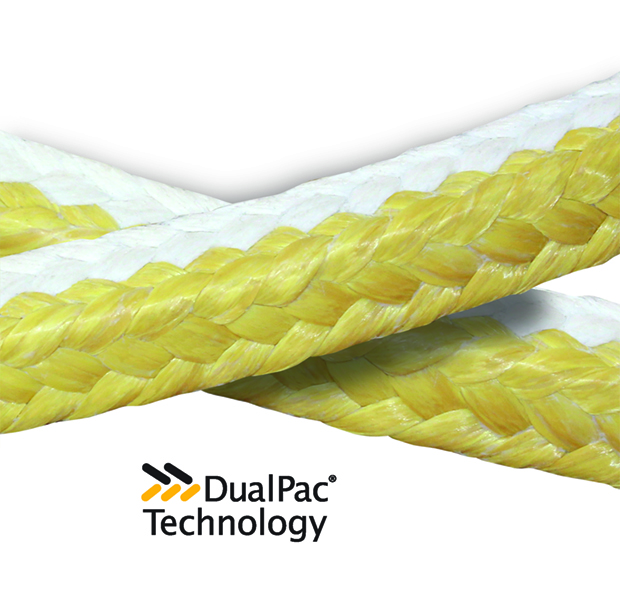
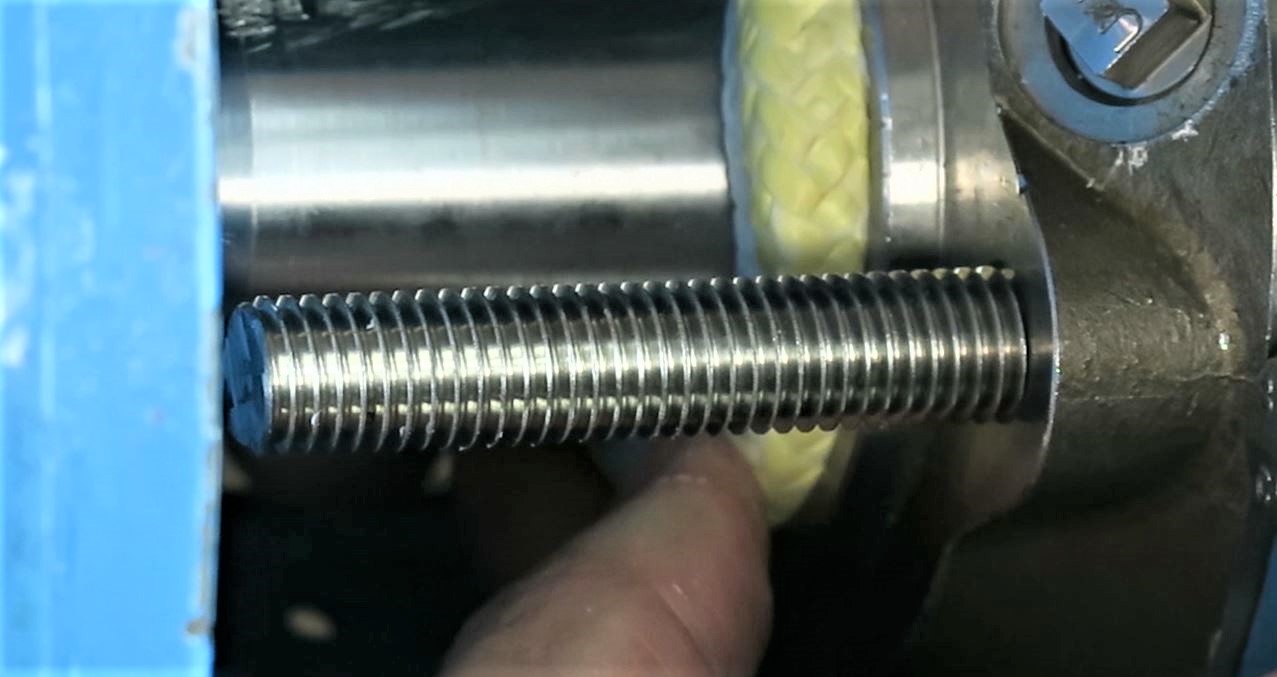
Packing: Overcoming the Challenges of Lantern Ring Replacement
One of the most significant hurdles during packing replacement is removing the lantern ring and the bottom rings. Lantern rings can become off-axis, bind up in the stuffing box, or get clogged with particulates, making removal difficult and time-consuming.
Why Leaving the Lantern Ring Unchanged Is Not Recommended
Despite these challenges, it’s not advisable to leave the lantern ring in place while only replacing the rings above. Here’s why:
Over time, the unreplaced bottom rings will wear, extrude, and consolidate, causing the lantern ring to move towards the bottom of the stuffing box and misalign with the lantern ring port.
This alteration prevents flush from reaching the ID of the packing, allowing solids to penetrate under the packing and dramatically reducing its lifespan.
A symptom of a misaligned lantern ring is heavy flush water leakage on the OD of the packing, indicating either misalignment or clogging due to intermittent or inadequate flush pressure, or dirty flush.
Solution: Eliminate the Lantern Ring
The solution to difficult lantern ring removal is straightforward—don’t use a lantern ring.
Our tests have shown that the first three rings of packing do the majority of the sealing, and the bottom rings mostly serve to keep solids out.
By using a throat bushing with built-in flush ports, you can eliminate the need to remove the lantern ring when you repack, and you’ll use less packing.
Since the top rings perform most of the sealing, you won’t sacrifice sealing capability.
To make the system more reliable, specifically engineered bushings are available that alter the water flow within the stuffing box to actively remove and exclude solids (e.g., SpiralTrac – Type P). This makes that the packing works in a clean environment, significantly extending it’s lifetime.
Pre-Cut Packing Rings: A Time-Saving Solution
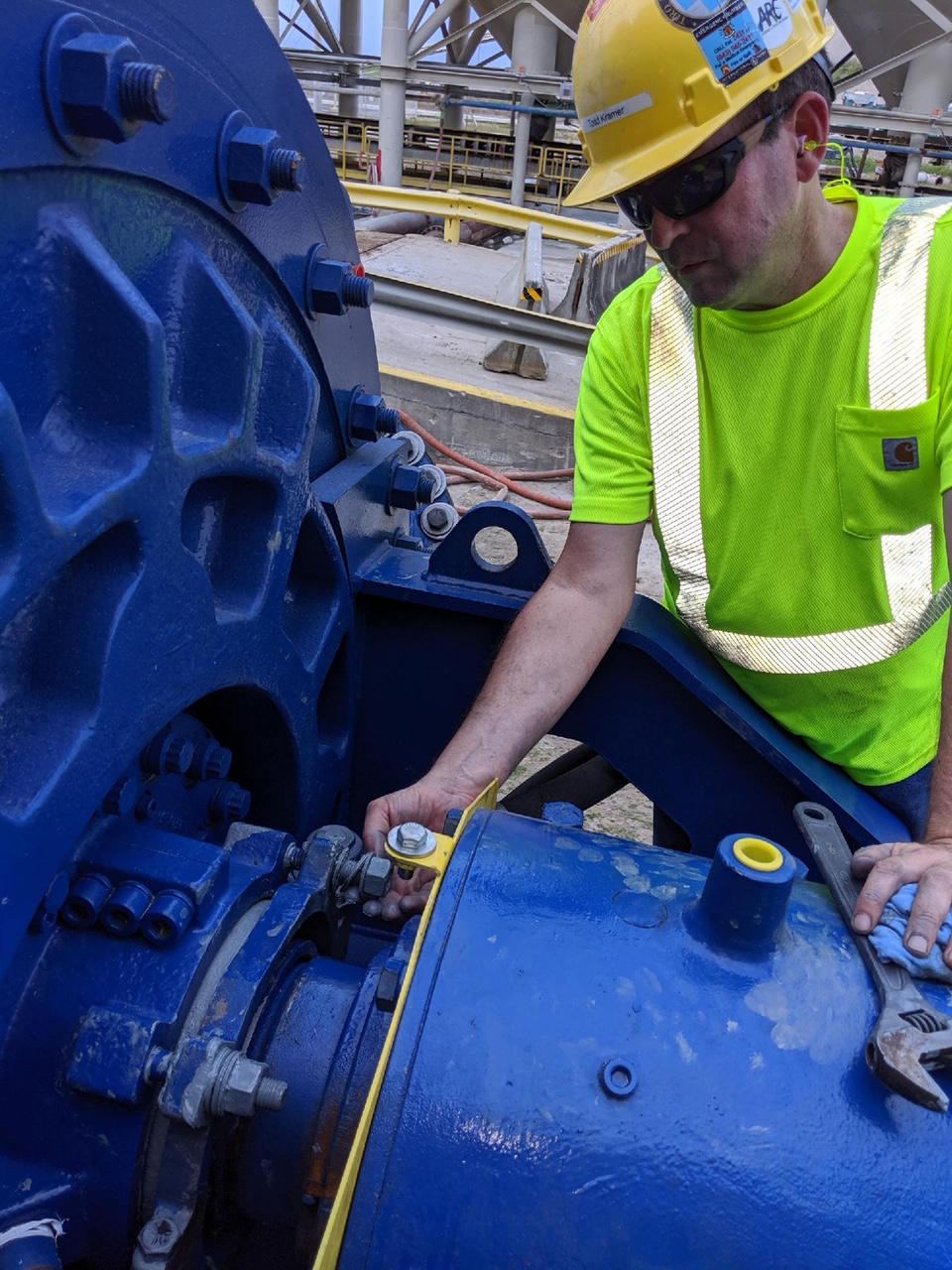
Another method to expedite slurry pump repacking is to purchase pre-cut rings. Most packing manufacturers now offer pre-cut rings for a small fee, which can be offset by eliminating the time and scrap required when cutting them yourself. These rings ensure correct sizing and accurate cuts made with a sharp blade.
Another method to expedite slurry pump repacking is to purchase pre-cut rings. Most packing manufacturers now offer pre-cut rings for a small fee, which can be offset by eliminating the time and scrap required when cutting them yourself. These rings ensure correct sizing and accurate cuts made with a sharp blade.
Mechanical Seals in a Slurry Environment: Selection & Environment
While modern cartridge mechanical seals are significantly easier to install than component seals, their installation still requires decoupling the power end and often moving pump/motor components. This can be time-consuming, particularly with large slurry pumps.
Advanced Split Seal Design: An Efficient Alternative
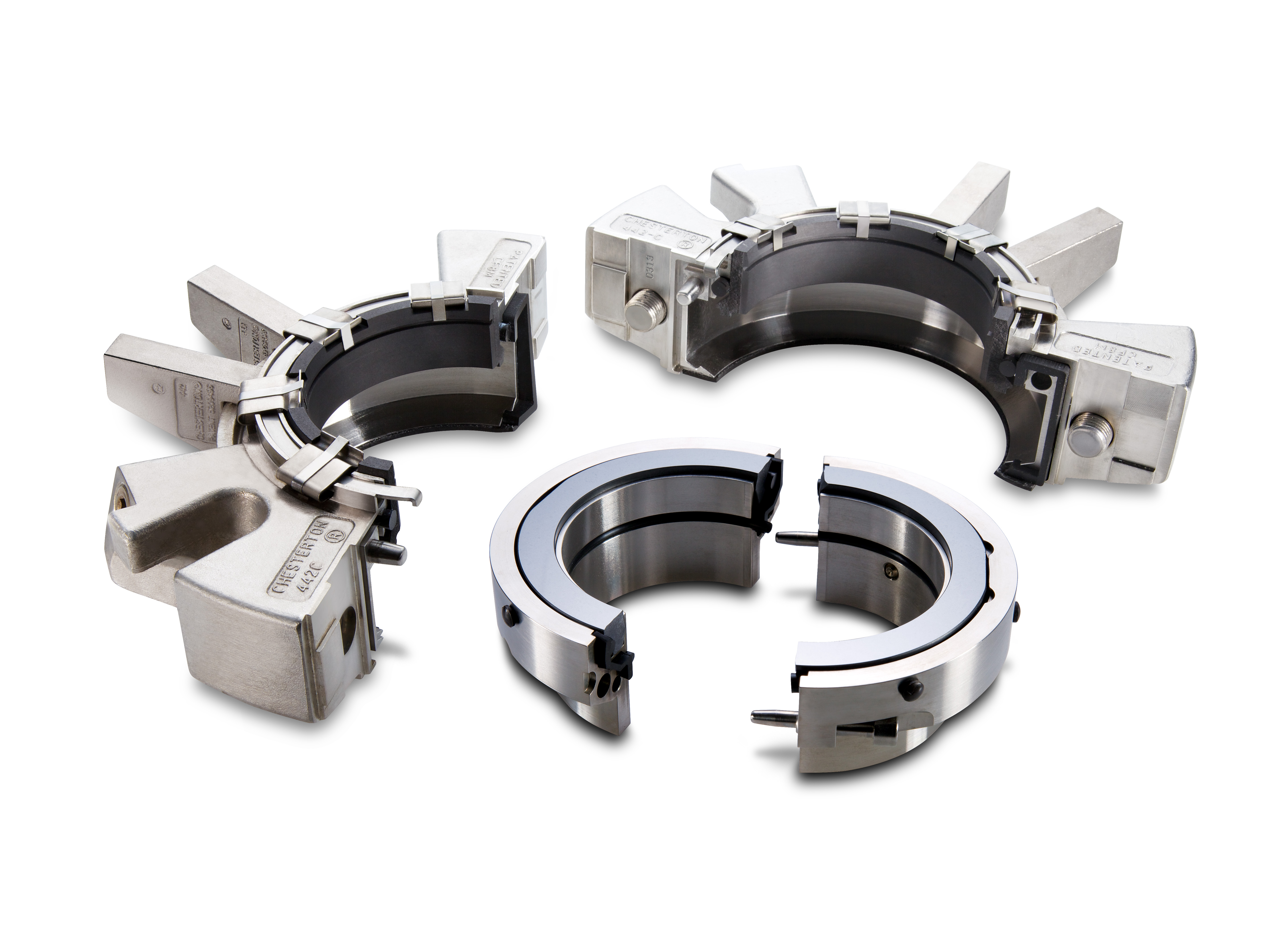
Over the past decade, advanced split seals like the Chesterton 442C Seal have evolved to have fewer components, making installation a matter of minutes rather than hours. This seal design can also now achieve seal life equivalent to a non-split seal. Newer features also include fully split O-Rings and easy field-repair capabilities.
Controlling the Seal Environment
Setting up appropriate environmental controls is critical when using Mechanical Seals in a slurry pump environment:
A clean flush is often required to keep control of contaminents in the stuffing box.
A bushing can be utilized to limit the amount of particulate that can get into the seal chamber. As with packing, there are engineered bushings designed to remove particulate from the seal chamber and help the seal operate in a clean fluid to improve seal life (Chesterton carries several varieties of these: the SpiralTrac Environmental Controller).
When a clean flush isn’t an option, heavy-duty slurry seals have dedicated features to withstand harsh slurry conditions. Typical Mechanical Seal features are line-on-line seal faces, non-clogging external springs, larger clearances to reduce clogging, and high-strength drives. These can often operate flushless under certain conditions, which can be improved with other environmental controls.
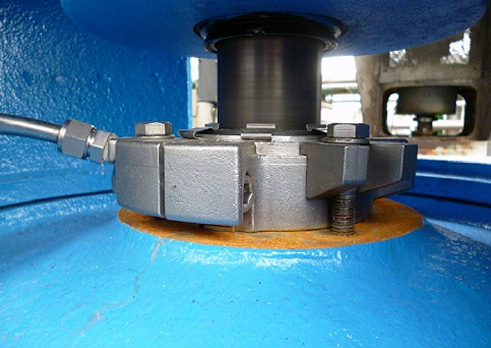
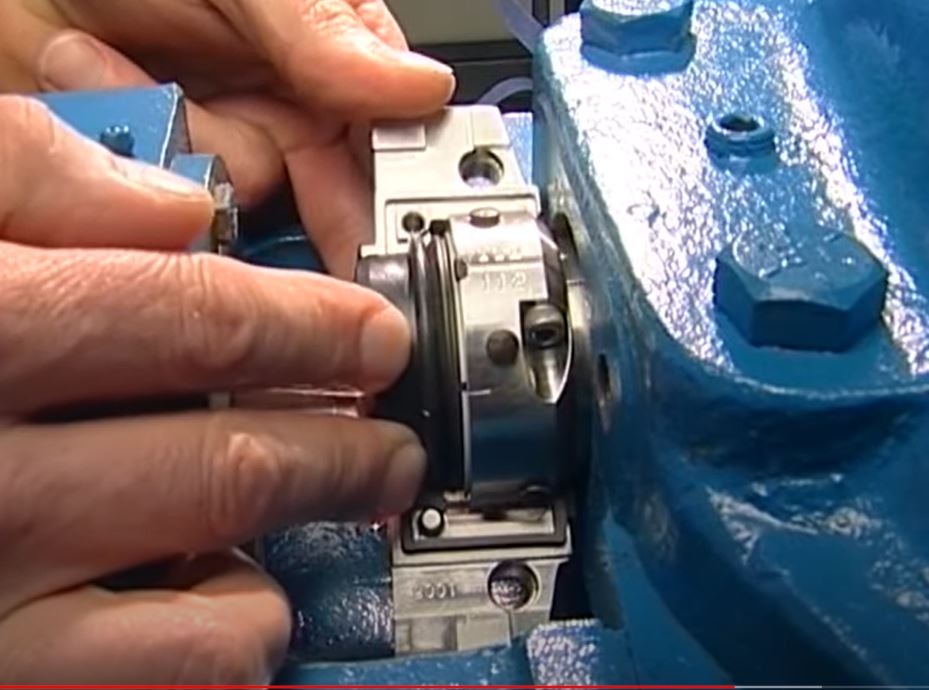
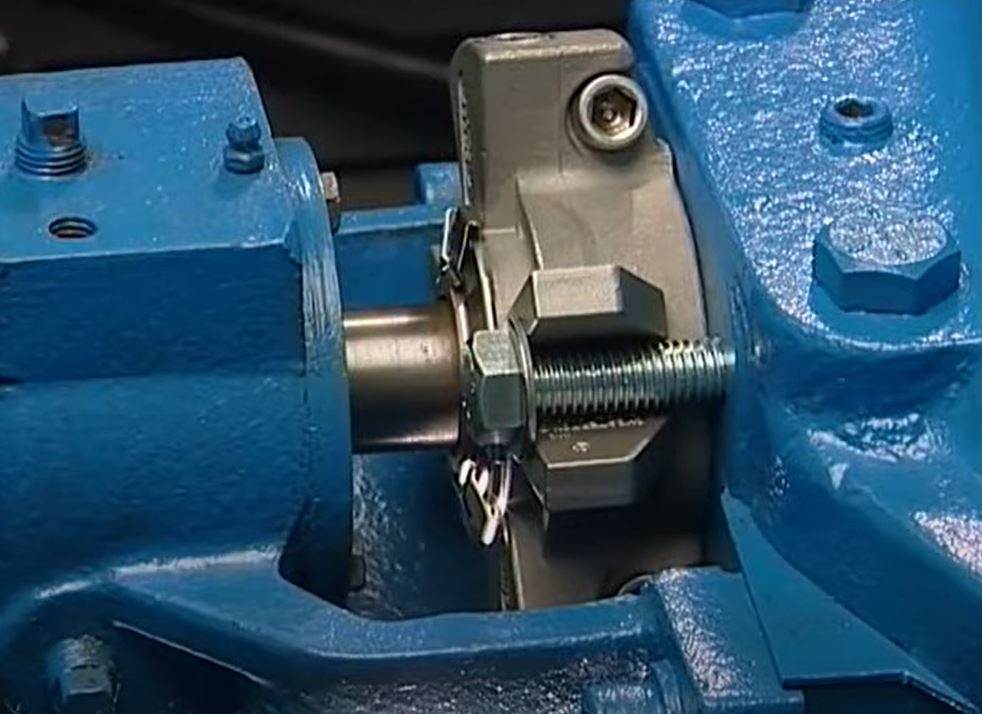
Other Methods of Improving Reliability and Reducing Maintenance
Aside from sealing considerations, there are many other ways to protect your assets and ease maintenance:
- Reinforced coatings can extend the life of pump internals and reduce equipment costs.
- Proper and automated lubrication extends bearing life along with adequate bearing seals.
- High-quality bolt and nut lubrication makes disassembly much easier.
By implementing these strategies, mining operations can streamline their slurry pump maintenance, reducing downtime and increasing productivity.
Please ask our Expert Desk for further information.
You can also make a preliminary selection using our product selector. Our product consultants will gladly assist you in selecting the ideal product for your application.